Environmental Engineering Reference
In-Depth Information
Table 6.5 Material properties
Material
Thermal
conductivity
(W/K-m)
CTE
(ppm/
C)
Density
(g/cc)
Modulus
(GPa)
Silicon (Si)
150
4.2
2.3
Gallium arsenide (GaAs)
50
5.8
5.3
Silicon carbide (SiC)
270
3.7
Aluminium (Al)
220
23
2.7
70
Copper (Cu)
393
17
8.96
110
Copper-tungsten (Cu-W) (10/90)
209
6.5
16.4
234
Copper-molybdenum-copper
(Cu-Mo-Cu) (13/74/13)
181
5.8
9.9
269
Beryllium oxide (BeO)
210
6.7
2.9
Aluminium nitride (AlN)
180
4.5
3.28
320
Aluminium silicon nitride (AlSiN) (30/70) 202
7
3
220
Metal matrix composite (MMC)
420
5.5
6.4
Aluminium-graphite-MMC
180
6.3
2.4
138
Copper-graphite-MMC
250-350
6.3-1.8
5.5
138-208
Beryllium-BeO-MMC
228-240
8.7-6.1
2.1-2.6
300-330
Figure 6.22, where the major subsystems in a power electronic package are defined.
In this figure, the relative fraction of total system cost by inverter subsystem is
summarized. Clearly, the cost is dominated by three clusters of subsystems: power
modules and gate driver, bus bar and sensors, and heat sinking and die casting.
A goal of power electronic development is to continue integration of the
power electronics into a full digital controlled IPEM module. Voltage rating plays a
key role in IPEM costs and relative breakdown. Figure 6.23 gives a cascade of
Pole A
Pole B
Pole C
Pole A
Pole B
Pole C
a
b
c
40 V
dc
R
R
L
L
L
a
b
c
R
(a)
(b)
Figure 6.21 Power stage based on discrete devices: (a) inverter schematic
and (b) FET arrangement on heat sinks
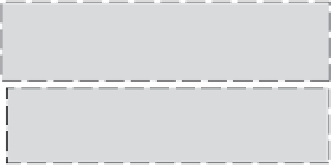







































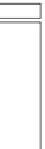























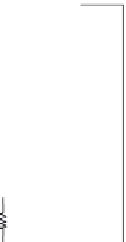




















































