Civil Engineering Reference
In-Depth Information
7.4 FINITE ELEMENT MODELING AND RESULTS
OF EXAMPLE 2
The second example presented in this chapter is for another simply sup-
in this study as G2 as shown in
Figure 7.8
.
Once again, the main objective of
the test was to investigate the ultimate moment resistance and ductility of the
composite girder. The structural steel used in the test was a high-strength
steel HPS70W having a nominal yield stress of 482 MPa (70 ksi). The gen-
eral layout and dimensions of composite plate girder G2 are shown in
Fig-
ure 7.8
. Similar to G1, the composite plate girder G2 had an overall length of
12,801 mm and a length between supports equal to 12,192 mm. The steel
plate girder had a web of 760.4
8.9 mm and upper and lower flanges of
182.6
19.6 mm. The measured flange and web portions of the steel plate
girder of G2 had yield and ultimate tensile stresses of 556, 700 MPa and 583,
B
P
6400.8 mm
1168.4
1854.2
1854.2
1133.5
85.7
304.8
(a)
Elevation
B
2184.4 mm
181
182.6×19.6
760.4×8.9
980.6
182.6×19.6
(b)
Cross section A-A
Figure 7.8 Elevation and cross section of composite girder G2.
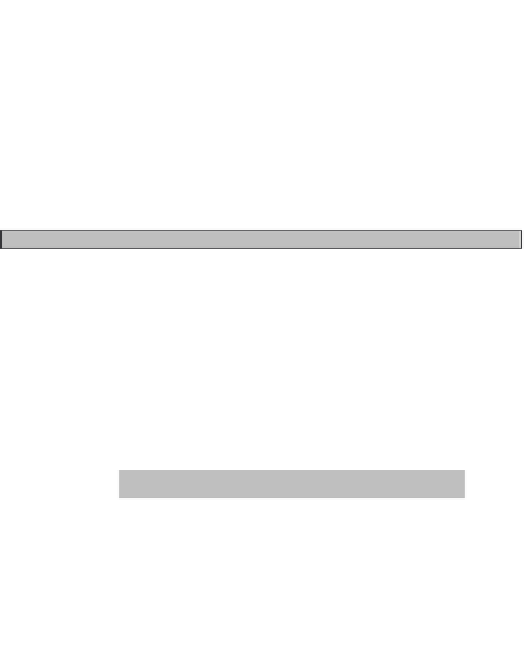






























































Search WWH ::

Custom Search