Biomedical Engineering Reference
In-Depth Information
h t
( )
h
y t
( )
y t
(
T
)
0
hs
hs
( )
1
sT
()
1
(1
e
)
K a
( )
s
o
r
where: T - spindle rotation period, μ - overlap factor, y(t) and y(t - T) - present
and past vibration amplitudes in the radial direction, Ф (s) - frequency
response function.
Stability lobes have been presented, showing that if the depth of cut
(DOC) and spindle speed are selected below the stability lobe, the process is
stable and if they are above the lobe, the process becomes unstable with
growing vibrations.
The issue of stability at high and low spindle speeds has been discussed
stressing the difficulty of defining the stability region for the low speeds due to
the complexity of modeling process damping (clearance angle becomes zero or
negative if there is a lot of waviness in the surface) (Figure 3).
Figure 3. Process damping mechanism in dynamic cutting [14].
Authors of this paper also deal with the complexity of the drilling process
suggesting that in drilling, the chisel has a ploughing action and the cutting
lips have a varying rake angle and chip thickness along the edge as well as
explaining that drilling forces and torque are a function of chip thickness,
width of cut, material properties, drill geometry and drill tip vibrations at the
current time and one tooth earlier. It has been stated that in order to predict the
cutting load when there are vibrations in the drill, the chip thickness
distribution along the cutting edge has to be identified considering vibrations
in every direction. These vibrations influence the cutting forces in drilling
therefore making it very challenging to solve the equation of motion:
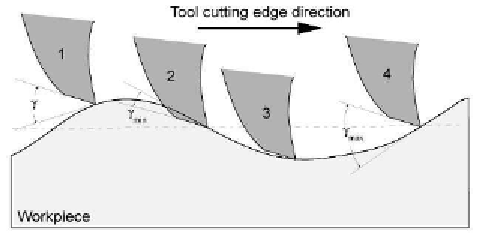

