Civil Engineering Reference
In-Depth Information
lapping the ends. Take time to bend the bars where
you need it, to keep them near the vertical center of
the footing. Then put the steps in, if any, and pour the
other half on top.
For ready-mix, you should have the reinforcing rod
and bulkheads in place. I use short lengths of bar
driven into the bottom of the trench, along with the
grade stakes, and fasten the long bars to them with tie
wires to keep them up off the ground. Let concrete
cure at least two days. In freezing weather, insulate
over the pour with straw or sawdust to keep in the heat.
⁄/¢"
Other Foundations
There are a few other options for building founda-
tions. A low-cost foundation can be constructed from
concrete block on a footing. You can leave it as is, if you
don't mind looking at it, or you can parge the block
with mortar to hide it. A poured-concrete foundation
is strong but ugly, and requires form work. Both can
be stone- or brick-veneered, set on the footing. How-
ever, building codes do not allow for the building
weight on the veneer.
A more expensive, but innovative, foundation is the
precast dense concrete foundation that is custom
designed for each house. The entire basement for one
log house we built was installed in three hours.
Installed with a crane, the 10-foot panels come with
Styrofoam insulation and studs predrilled for electric
wiring. The panels can include basement steps, foun-
dation for a chimney, ledges for stone or brick veneer,
ledges for the floor-joist system, windows, and doors.
Covering exposed concrete foundations with stone
veneer requires the use of masonry mortar (which is
different from footing mixture). I use a mix of one part
masonry cement to three parts sand, and I use one
part lime to two parts Portland to make the masonry
cement — that's one part lime, two parts Portland, and
nine parts sand. There are lots of other formulas, but
this has worked nicely for me over several years. And
it's cheaper than buying masonry cement or premix.
Mortar should be thoroughly mixed in a box or
wheelbarrow with a hoe, using enough water for a
slightly stiff mix. Most masons use it as dry as possi-
ble to avoid smearing and running, but it bonds to the
stone better if it's wet ( just dry enough not to run).
The floor joists can be set directly on the foundation ledge inside the
first logs, eliminating the need for attaching to the sill. Both the sill
and the joist end must be set on either metal flashing or pressure-
treated wood to act as a termite shield.
I don't mix masonry mortar in a cement mixer
unless I have plenty of help and plan to use many
batches. You'll find that if you work alone or with one
helper, it takes quite a while to use up a couple of cubic
feet of mortar, and you may mix but one or two
batches a day. Also, a lot of it gets caught in the tines
of the mixer and wasted when you wash it out.
Both concrete and mortar must be kept moist for
several days to complete the chemical reaction that
produces strength. Just letting it dry out doesn't work.
Wet burlap sacks are good to cover fresh work, or
sheet plastic. Spray with water, but not until the sec-
ond day or you'll wash it away.
And just don't do mortar or concrete work in freez-
ing weather. Portland cement generates a little heat
the first day as the chemical action goes on, but it's
only good to about 30°F. It's best to use insulation and
sheet plastic to hold heat and ground temperature
next to the work the first two cold nights.
Below 28°F or so, just don't lay stone or build ma-
sonry aboveground. The chill will permeate even insu-
lation in time, which will freeze your work. Footings
down in the ground, with some straw over them for
insulation, can be poured safely down to about 20°F.
I don't use antifreeze solutions in mortar or concrete.
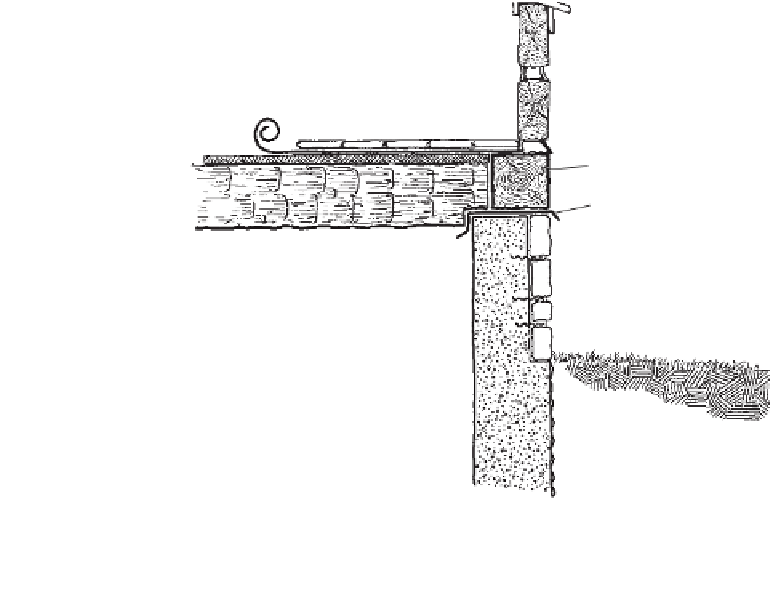
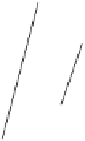






