Civil Engineering Reference
In-Depth Information
time operation. When each section was poured and set
up, we went on to the next, leaving rebar extending to
tie the sections together.
A contractor I know once dug out too much for this
operation and the basement wall fell in, leaving a hole
you could drive a truck through. Brick damping had
so weakened the basement walls that, as a result of this
mishap, the owner decided to demolish the entire
1840s house. It wasn't a log house, but a huge, beau-
tiful Italianate-style brick plantation house, which
cracked and settled in a way logs would not have.
Preparing for the Log Setup
With either a basement or a continuous foundation,
you can actually do away with sill logs, which gener-
ally support the floor joists. Historically, the joists
were notched into the sills. Today, many builders use
galvanized metal joist hangers. You may leave a wide
foundation, with the first log at the outside and the
ends of the joists on the inside, resting on the masonry
itself. The first log is below floor level, as is the sill, but
it doesn't have to support the floor.
Bring your foundation up a foot or more off the
ground before you lay the first log. Eighteen inches is
better, because termites don't like to travel far from
ground moisture. And you want that much crawl
space. After the logs are in place, fill in any gaps to give
more support, using mortar and stone where needed.
And use metal flashing between the foundation and
the first logs.
I am often required to set heavy bolts into the foun-
dation masonry to anchor the sill logs. This is com-
monly done in conventional stud-wall construction
and in post-and-beam construction. It would be of no
value in a log house, however, unless some way were
devised to fasten all the logs together, from the foun-
dation on up. The weight of the logs themselves holds
the house together, and I have never seen a dovetail-
notch cabin blown apart by wind. (The roof might
depart in a really heavy gale, but we talk about how to
prevent that in the chapter on roofs.) But building
codes often require anchor bolts. And they do help
keep the sill logs in place laterally.
Set first logs and joist ends on metal flashing or on
pressure-treated wood (building codes allow either) to
Perforated drainpipe must be laid around a basement wall below floor
level to carry away groundwater. Gravel and filter fabric are necessary
to keep backfill soil from clogging the pipe.
Basements must be sealed against moisture all the way up the walls,
which will be backfilled. Drainpipe, in conjunction with the sealant,
will keep water from soaking or seeping into the basement walls.
foil termites and stop moisture damage. Moisture
wicks up from the ground, through the foundation,
and the flashing stops it. The treated wood doesn't
stop moisture penetration, but the poison of the treat-
ment kills both the rot fungus and hungry termites.
Aluminum or galvanized flashing will work, but we
use copper. It ages into invisibility and, being thicker,
lasts longer. But it costs more too. (Depending on the
market rate per pound, it costs from $200 to $300 for
a 2-by-50-foot, 100-pound roll.)
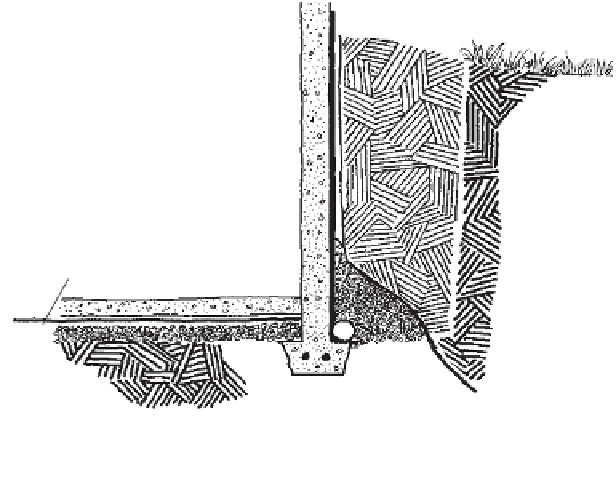

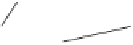
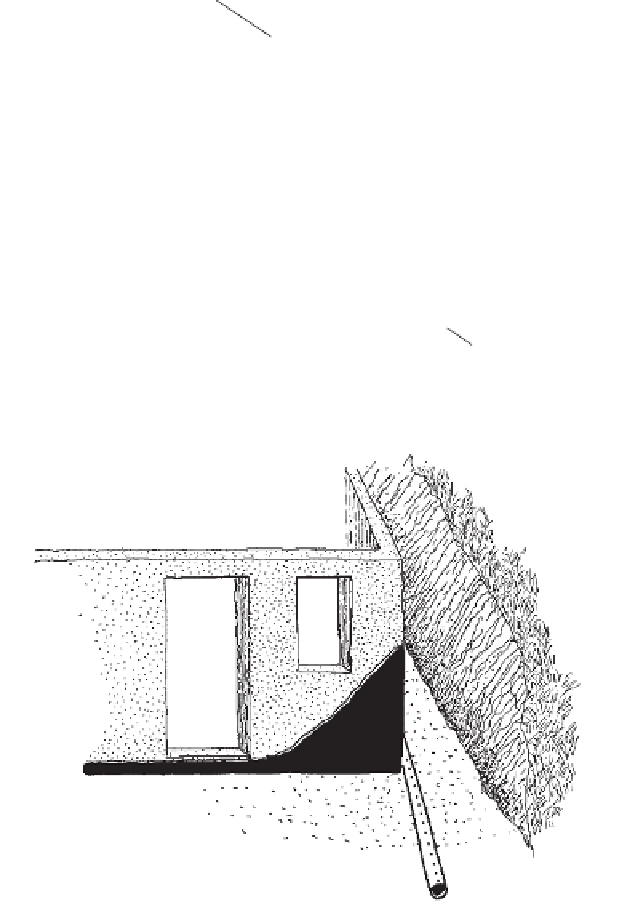


