Biomedical Engineering Reference
In-Depth Information
made by glass, and then peeled off from the substrate after PDMS
is solidiied for subsequent biochip fabrication, e.g., serving as the
chip cover. Besides that, some of silicon-based biochips/biodevices
are popular due to their integration ability with CMOS circuitry
[2, 3]. Researchers also directly work on glass slide as biochip
substrate. For example, metal electrodes are deposited on glass
slides for manipulating electrochemical reaction. However, the key
components of the chips (e.g., low channels or electrodes) need
well-delineated patterns. Photolithography plays an important role
to achieve these fabrication results. The purpose of this operation
includes two aspects. Firstly, it is to create on the substrate surface
a pattern whose dimensions are close to the design requirements as
possible. Secondly, the multiple designed patterns correctly place on
the wafer surface and the individual parts are in the correct positions
relative to each other [4, 5]. Figure 6.1 shows the low chart of the
photolithography. To explain this technology in detail, four major
process steps: (1) substrate cleaning, (2) photoresist selection and
application, (3) mask fabrication and alignment, and (4) photoresist
exposure and development are mentioned as following:
Clean substrates
Clean substrates
Apply photoresist
Apply photoresist
Soft bake
Soft bake
Deposit
new layer
Deposit
new layer
Align photomask
Align photomask
Expose pattern
Expose pattern
Strip
photoresist
Strip
photoresist
Develop photoresist
Develop photoresist
Etch
Etch
Hard bake
Hard bake
Inspect
Inspect
No
Photolithography process flow
No
Photolithography process flow
Yes
Yes
Figure 6.1
Photolithography process lowchart.

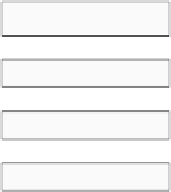

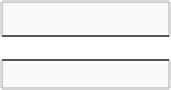
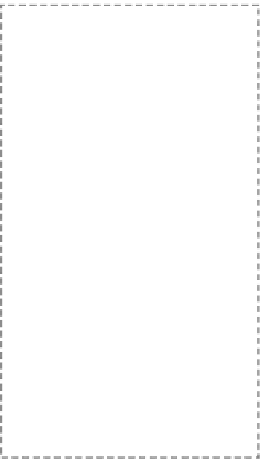
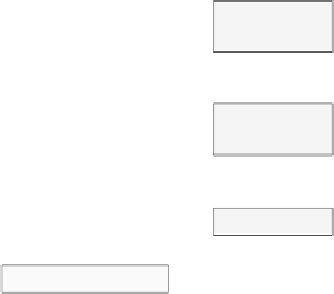















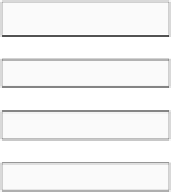



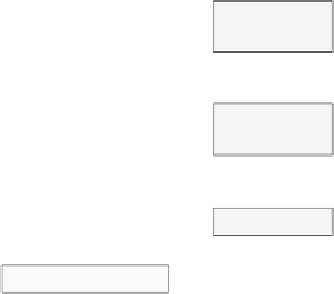




































Search WWH ::

Custom Search