Biomedical Engineering Reference
In-Depth Information
FIGURE 7.37
Mixing pattern in a circular chamber: (a) first mode (
m¼
0,
n ¼
1,
f
*
¼
1.000); (b) second mode (
m¼
1,
n ¼
1,
f
*
¼
1.594).
(Redrawn after experimental data of
[50]
.)
propagation. Due to viscous losses, the first-order particle velocity decays exponentially, 7.38 (c).
Therefore, only a fast moving fluid layer exists next to the membrane, 7.38 (d). A basic FPW-device
consists of rectangular flow channel that has a thin membrane on the bottom. The composite
membrane is made of low-stress silicon nitride, piezoelectric zinc oxide, and aluminum. Typical
membrane thicknesses range from 1 to 3
m
m. The FPW have a typical frequency of 3 MHz and
a wavelength of 100
m. Arrays of finger pairs placed at wavelength intervals on a piezoelectric film,
generate the flexural waves.
Rife et al. used acoustic streaming to improve mixing
[52]
. The actuation system is based on an
array of piezoelectric actuators. The actuator consists of a BaTiO
3
piezoelectric thin film. The whole
piezoelectric actuator was deposited as a thin film on a silicone substrate. Electrical contacts are made
with gold and platinum electrodes. The piezoelectric thin-film thickness was chosen so that
the actuator works with the fundamental thickness mode resonance near a frequency of 50 MHz. The
attenuation length was about 8.3 mm, which can cover the length of the mixing channel. The
microchannel network is shown in
Fig. 7.39
(a). The actuator array was attached to the PMMA device,
which contains the microchannel network. Thus, the actuator is facing air on one side and liquid on the
other side. Due to the large mismatch of acoustic impedance on each side, the acoustic energy is almost
entirely reflected at the air side. Almost all of the acoustic energy is transferred into the fluid. At the
resonance frequency of about 50 MHz, the actuator can induce a flow velocity of 1 mm/s.
Yang et al. reported an acoustic micromixer with an actuator membrane
[53,54]
.
Fig. 7.39
(b)
shows the schematic concept of the device. As discussed in the previous section, the different
vibration modes of the actuating membrane can induce flows with different streamline patterns. The
mixing chamber was fabricated in a Pyrex glass wafer, which is bonded to silicon using anodic
bonding. The mixing chamber measured 6 mm on each side and is 60
m
m deep. The actuating
membrane is formed in the silicon wafer using anisotropic etching with KOH. The membrane is
m
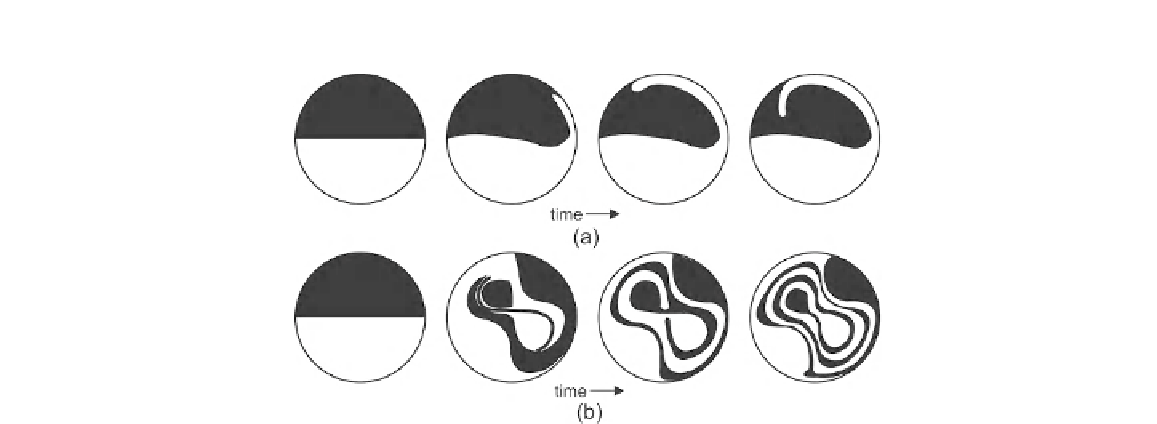



Search WWH ::

Custom Search