Information Technology Reference
In-Depth Information
different calculated characteristic values over the cutting edge like the gradient of the
chip thickness Δh
cu
/Δl
s
. This gradient, for example, represents the compression and
squeezing of the chip over the cutting edge. Thus, this value can be used for the anal-
ysis of the tool load at the cutting edge.
The comparison of the calculated new characteristic value and the tool wear from
cutting trials show good correlations. The localization of tool wear as well as a qualit-
ative comparison of different processes regarding the expected tool life is possible.
E.g. the tool life behavior of full profile blades and half profile blades correlates well
with the simulation results.
In the future the manufacturing simulation has to be enhanced in order to calculate
the expected tool life for bevel gear cutting. This, for instance, can be applied for
increasing the productivity of the cutting process and for optimizing the process de-
sign regarding tool changes. Thus, the development of a tool life model for the bevel
gear cutting process has to be realized. In a first step analogy trials in single flank
cutting on a lathe will be performed, see figure 14.
Determination
of Endured
Load Cycles
Transfer to
Multi Flank
Application
Analogy Trials
(Turning Process)
Verification
v
c
v
c
slotted
workpiece
tool
load cycles N [-]
cutting edge length l
s
[mm]
load cycles N [-]
Tool Life L = f (h
cu
, l
e
,α
e
, γ
e
, v
c
)
Fig. 14.
Methodology for prediction of tool life in bevel gear cutting
Here the influence of chip thickness h
cu
, working length l
e
, working relief angle α
e
,
working rake angle γ
e
, cutting velocity v
c
and tool coating will be investigated. Af-
terwards a determination of the endured load cycles over cutting edge length will be
conducted in step 2. With the load cycles a hands-on visualization will be realized. A
transfer to multi flank application will be done in step 3. Here the presented characte-
ristic value K
G
will be used to consider the additional load at the corner radius of the
tool due to multi flank chips. Finally industrial cutting trials will be performed in
order to optimize and verify the tool life model. Further the tool life model will be
implemented in the manufacturing simulation.
Acknowledgements.
The authors would like to thank the German Research Founda-
tion (DFG) for supporting the presented works, which are part of the research project
“Methodik zur Vorhersage der Werkzeugstandzeit bei Fertigungsprozessen mit
Mehrflankenspänen am Beispiel des Kegelradfräsens”.
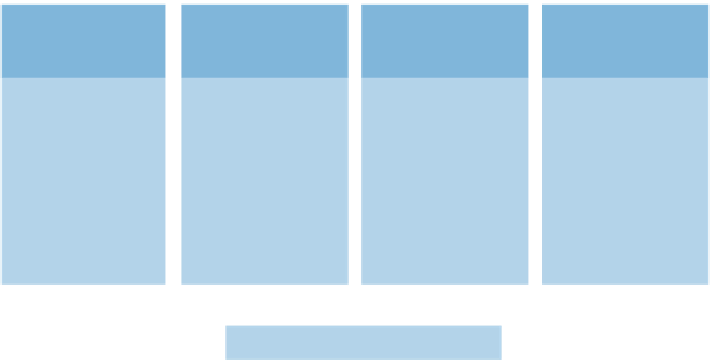





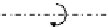




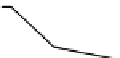










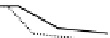


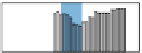


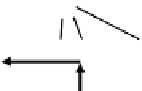

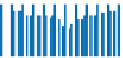
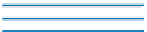

Search WWH ::

Custom Search