Information Technology Reference
In-Depth Information
coefficients. E.g. the coefficient a
χ
is a time invariant value therefore a positioning of
the cutter, whereas u
χ
is linearly time-dependent:
χ
m
)
2
+ d
χ
⋅
m
)
3
+ e
χ
⋅
m
)
4
+
(
α
,
ω
) = a
χ
+ b
χ
⋅
(
α
-
α
m
) + c
χ
⋅
(
α
-
α
(
α
-
α
(
α
-
α
α
m
)
5
+ g
χ
⋅
α
m
)
6
+ p
χ
⋅
ω
m
)
2
+ r
χ
⋅
ω
m
)
3
(1)
f
χ
⋅
(
α
-
(
α
-
(
ω
-
ω
m
) + q
χ
⋅
(
ω
-
(
ω
-
ω
m
)
4
+ t
χ
⋅
ω
m
)
5
+ u
χ
⋅
ω
m
)
6
+ s
χ
⋅
(
ω
-
(
ω
-
(
ω
-
γ
Cutter Head
β
τ
Workpiece
η
ω
Theoretical
Cross Axis
Point of Gear
φ
mccp
ε
α
χ
Fig. 2.
Scheme and axis movements of a bevel gear cutting machine
2.2
Modeling of Workpiece and Tool
In the simulation the workpiece and the tool envelope are modeled as 3D clouds of
scattered points. With these points a mesh of triangles is generated for the workpiece
and the tool. The modeling of the workpiece can be described in three steps, see
figure 3. At first the cross section of the gear flank is defined by four points. With
these points the gear width b, the toe and the heel of the bevel gear are defined.
Cross Section of the Gear Flank
Extrusion of Cross Section around the central axis
4
3
360°
toe
b
4
b
heel
1
3
1
2
2
Triangulation of Surface
Fig. 3.
Modeling and triangulation of workpiece









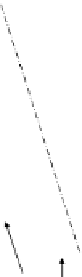

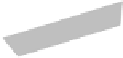






















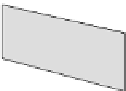




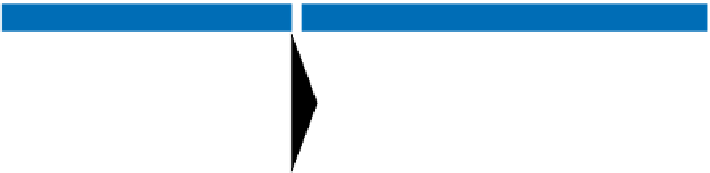


















Search WWH ::

Custom Search