Information Technology Reference
In-Depth Information
tool wear and tool life, see [1]. Currently it is not possible to analyze the bevel gear
cutting process sufficiently regarding tool wear and tool life, because of its complexi-
ty. Hence, the design of the cutting process happens iteratively in order to find the
optimal process parameters. So an exact knowledge about the tool wear and tool life
behavior is necessary to optimize the cutting process. These challenges and issues are
presented in figure 1. In order to provide a simulation tool for analyzing and optimiz-
ing the bevel gear cutting process a manufacturing simulation has been developed at
WZL, as presented by [2-3].
Manufacturing Process
To o l W e a r
High Local Tool Wear
Critical Wear Behaviour
Low
Process
Stability
Production Stops
(e.g. Tool Changes)
Iterative Process Design
(trial-and-error)
Source: Klingelnberg
Complex Process Kinematics
- Plunging Process
- Generating Process
Different Tool Concepts
Fig. 1.
Challenges in bevel gear cutting
2
Modeling and Simulation Method
Within the manufacturing simulation a geometrical penetration calculation is con-
ducted as described by [2-4]. Before starting the calculation the kinematics , work-
piece and tool have to be modeled as described below.
2.1
Process Kinematics
All axis movements, like in the real cutting process, can be considered in the simula-
tion. In figure 2 the axis movements and positions of the bevel gear cutting machine
are presented. More precisely, the variables and the resulting movements are: mccp
(the machine center to cross axis point), α (cradle angle), β (modified roll by work-
piece rotation), γ (angular Motion), φ (radial motion), ε (horizontal Motion), η
(vertical motion), χ (helical motion), ω (tool rotation). All axis movements can be
described as a series expansion, which is truncated after the sixth order, regarding the
mean tool angle ω
m
and the mean cradle angle α
m
.
For example the axis movement for the depth position χ of the cutting tool , so
called helical motion, is calculated by formula 1. The variables a
χ
to u
χ
represent the

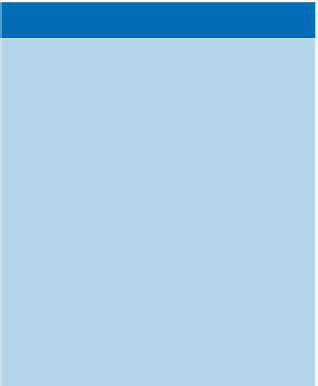

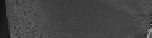
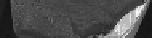












Search WWH ::

Custom Search