Biomedical Engineering Reference
In-Depth Information
Ion implantation is a process in which virtually any element can be injected into the near-
surface region of any solid. However, surface atoms will be removed by collisions between the
incoming particles while atoms in the near-surface layers of a solid are removed by a process called
sputtering, as shown in Figure 19.6. Sputtering sets the limit of the maximum concentration of
implanted atoms that can be retained in a target material. The yield of sputtered atoms, that is, the
number of sputtered atoms per incident ion, typically lies in the range of 0.5-20 depending upon
ion species, ion energy, structure and composition of the target material, and experimental geom-
etry [20,21]. Therefore, a high ion sputtering yield will result in a thin modifi ed layer and a reduced
retained dose.
Ion implantation has the ability to alloy any elemental species into the near-surface region of
any substrate, irrespective of thermodynamic constraints such as solubility and diffusivity. These
considerations coupled with the possibility of low-temperature processing have prompted explo-
ration into applications where the limitations of dimensional changes and possible delamination
associated with conventional coatings are the areas of concern. Interests in nonsemiconductor
implantation have expanded from the initial friction and wear studies to other areas such as corro-
sion, oxidation, fatigue, conductivity, optical, and biomedical applications. In addition to metals,
polymers and ceramics are receiving more attention from researchers with the principal objectives
of increasing the conductivity, wettability, surface energy, and adhesion of polymers and investigat-
ing the fracture toughness and tribological properties of ceramics.
19.2.3 D
EPOSITION
P
ROCESS
AND
D
YNAMICS
Plasmas used for deposition can be either single species or multiple species. Reactants in the plasma
will diffuse to the substrate surface giving rise to chemical reactions and thin fi lm deposition, and
the details are illustrated in Figure 19.7. The parameters of the deposition process such as deposi-
tion rate and thin fi lm structures can be varied by adjusting the working pressure and modes of
substrate biasing [19,22-24]. RF, DC, and pulsed biases are the common modes of substrate biases.
Typically, RF and DC biases are in the range of 0 V-1 kV while pulse biases can be varied from
low-voltage thin fi lm deposition to high-voltage ion bombardment. Bombardment with energetic
particles has been observed to enhance a number of fi lm characteristics and properties that are criti-
cal to the performance of thin fi lms and coatings such as adhesion, densifi cation of fi lms grown at
low substrate temperature, and modifi cation of grain size and morphology, optical properties, and
hardness and ductility.
Gaseous plasmas, such as hydrocarbons, methane, ethane, ethylene, acetylene, and benzene,
are widely used in the synthesis of plasma-polymerized hydrogenated carbon fi lms. In plasma
Main plasma flow
Pumped out
Transfer of
reactants to surface
Transfer of by-products to main
Absorption of
reactants
Desorption of by-products
Surface diffusion and reactions
Substrate
FIGURE 19.7
Schematic diagram of the sequential steps of deposition process.











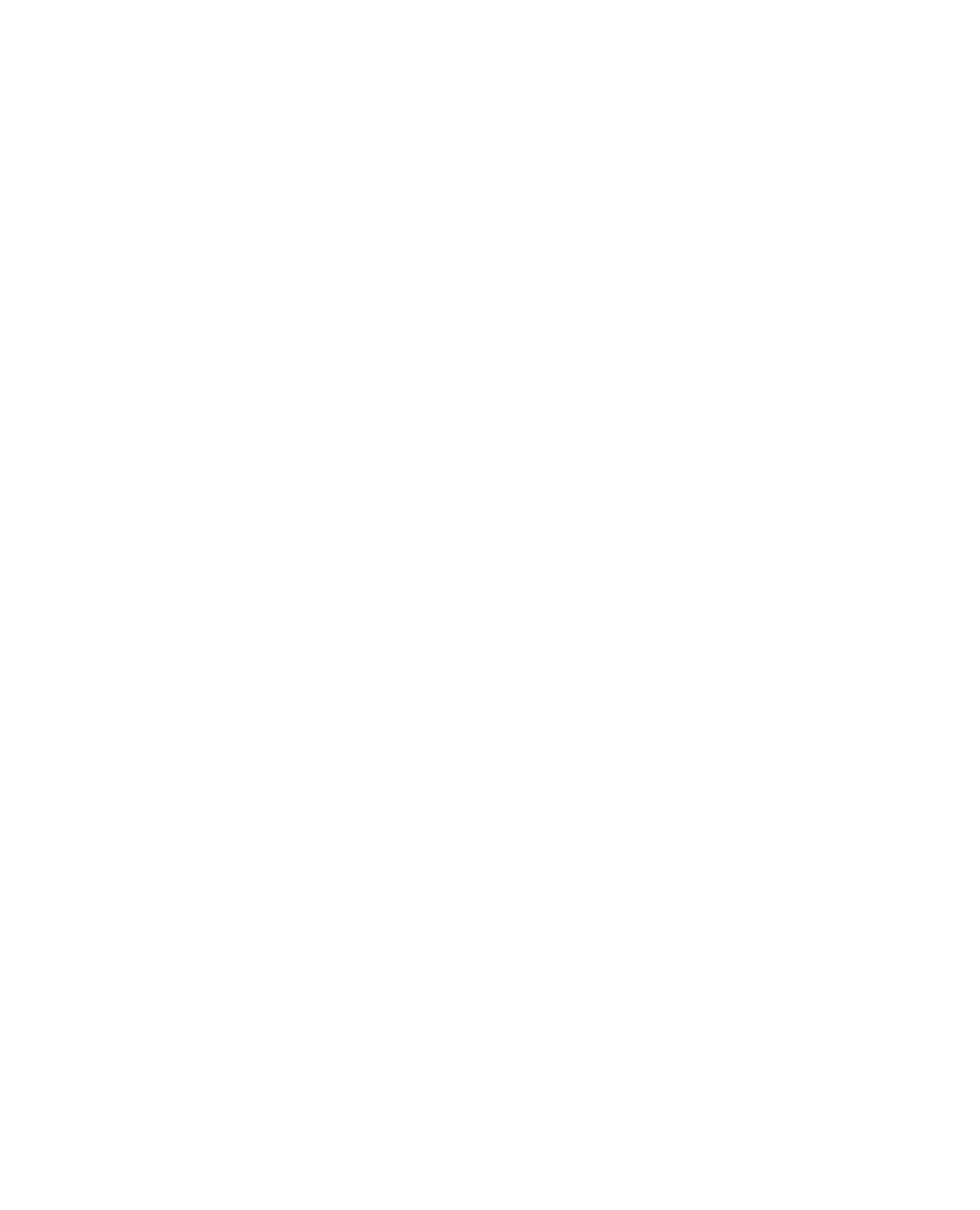