Biomedical Engineering Reference
In-Depth Information
(A)
(B)
FIGURE 13.14
Forces exerted by expanding polypyrrole are represented as arrows. (A) The lateral forces
are not countered and will result in delamination after few cycles. (B) The lateral forces are countered by
Au post.
Evaporated and patterned
a layer of Au with adhesion layer of Ti
Electroplated Au through resist opening
Deposited PECVD SiO
2
Removed the photoresist
Defined photoresist wells
and etched SiO
2
to expose Au
at working and counter electrodes
Electropolymerized polypyrrole
FIGURE 13.15
Microfabrication process for polypyrrole actuator—the active component in a microfl uidic
valve.
PPy was then electropolymerized on these posts, completely surrounding them, which reduced
the possibility of delamination during operation. In addition, the gold posts were left with a rough
top surface, which further improved adhesion between gold and PPy.
13.3.2.1
Microfabrication of the Active Part of the Microvalve
The active component in this microvalve is the PPy microactuator. The microfabrication process
sequence on a glass substrate is as follows (see Figure 13.15).
First, an adhesion layer of Ti (10 nm) is thermally evaporated onto a glass substrate. Then, a
conducting fi lm of gold of 400 nm thickness is thermally evaporated on top of Ti, and both metals
are photolithographically patterned to form WE and CE as well as metal traces to contact pads.
An insulating silicon dioxide fi lm of 500 nm thickness is deposited via plasma enhanced chemical
vapor deposition (PECVD). SU-8(5) photoresist is then spin-coated onto the oxide to a thickness
of 2 µm, exposed and developed to open up resist wells over the electrodes. The exposed area of
the WE is a 40 µm square while the exposed area of the CE is a 40 µm wide semicircular strip
surrounding the WE. Oxide in these wells is etched away, and more gold is electroplated in the
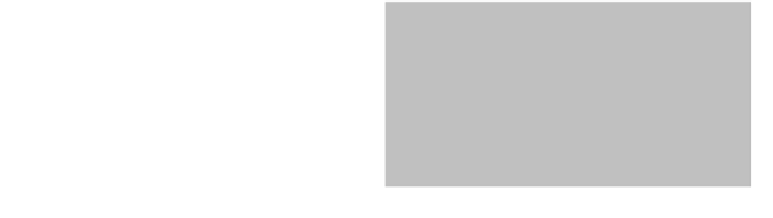
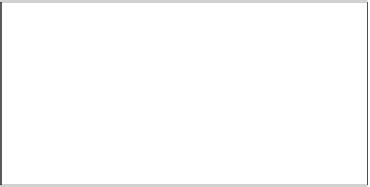



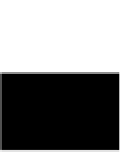










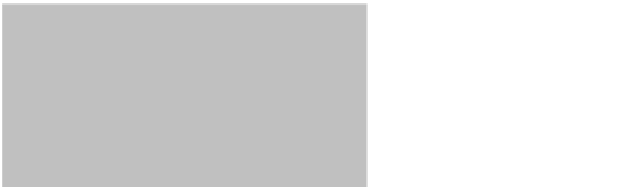









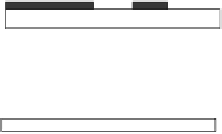


















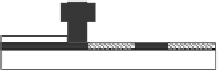


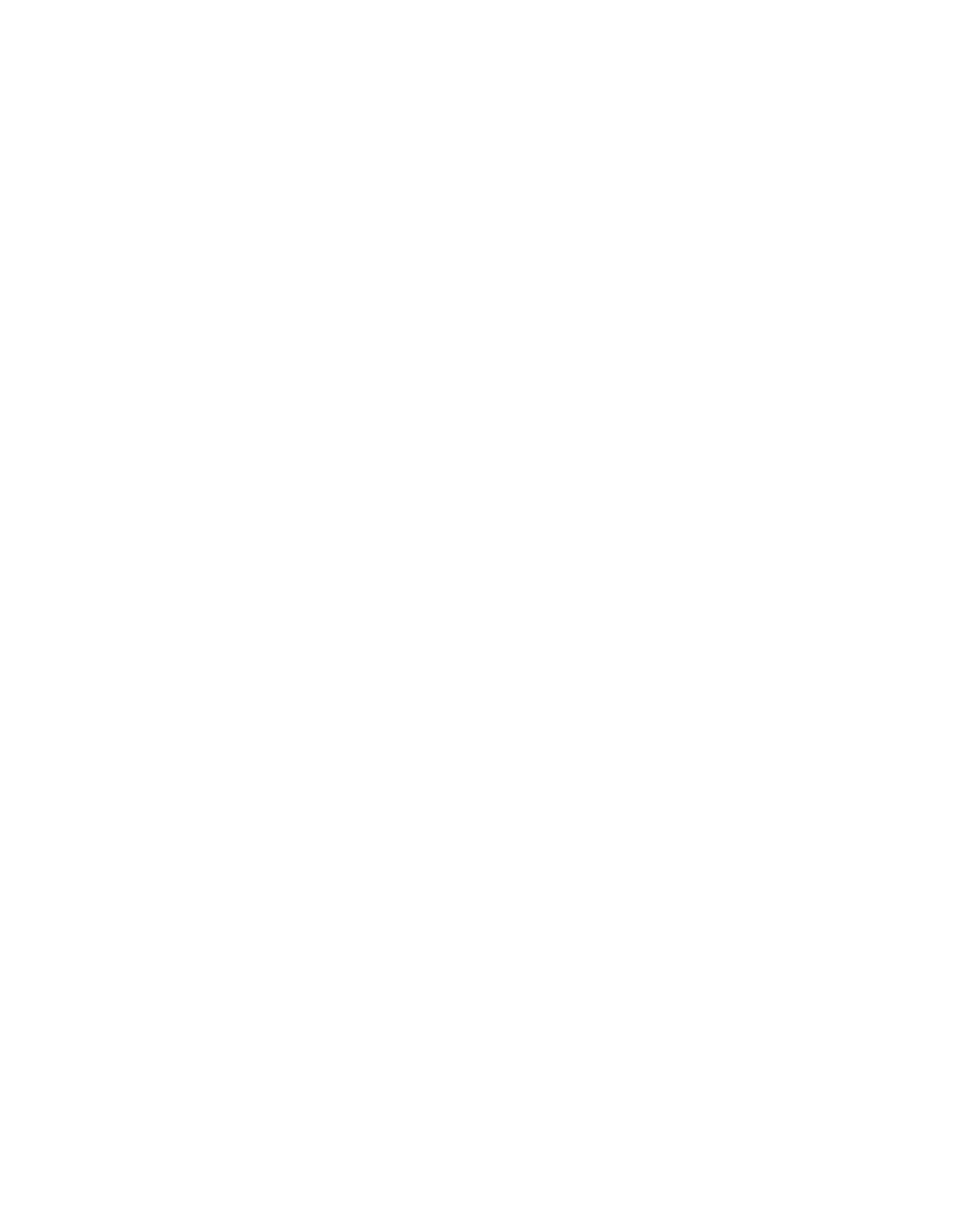











