Biomedical Engineering Reference
In-Depth Information
Apart from the slurry-immersion coating, electrospray coating techniques have also been
applied together with the polymer-sponge process to produce ceramic foams, for example, Al
2
O
3
[175] and ZrO
2
foams [176]. Unlike the foams produced by the slurry-immersion method, the struts
of the ceramic foams produced by the process of electrospray coating contain fewer holes and
cracks. This microstructure can lead to improved mechanical properties of the foams [176].
Another possibility investigated to improve the mechanical properties of foams made by the rep-
lication method is to apply a thin polymer coating on the porous structure. For example, to improve
the mechanical stability of highly porous Bioglass-derived scaffolds produced by the replication
technique [80], a polymer coating, such as poly(d,l-lactic acid) (PDLLA), was applied [177]. The
coating thickness was approximately 3 µm on an average. Although the thin coating layer did not
increase the mechanical strength of the foams considerably, it signifi cantly improved the mechani-
cal stability of the structure. The fracture energy of the coated foams was
20 times higher than
that of uncoated foams. More importantly, upon immersion in SBF, nanofi bers of hydroxyapatite
deposited within the PDLLA coating layer, eventually a nanocomposite layer, formed biomimeti-
cally on the strut surfaces. This method has remarkably improved the mechanical performance of
the scaffolds in a biological environment [177].
Gelcasting
.
This method adopts one of the direct-foaming techniques mentioned in Table 1.10
to achieve highly porous green bodies. The foamed suspension is set through a direct-consolidation
technique, listed in Table 1.10, that is, polymerization of organic monomers (i.e., gelation), in which
the particles of the slurry are consolidated through polymerization reaction. A green body is formed
after the gel is cast in a mold [178-180]. Figure 1.5 gives the fl owchart of the gelcasting process.
Two factors are critical in the gelcasting process: (1) the gelation speed must be fast enough to
prevent foam collapse, and (2) the gel rheology is important because the process involves casting.
Systems of high fl uidity are required in order to enable easy fi lling of small details in molds to allow
production of high-complexity shapes. Gelcasting techniques have been applied to produce hydroxy-
apatite foams [181-183]. Gelcasting has also been combined with the replication process (described
above in this section) to produce hydroxyapatite scaffolds with interconnected pores [184].
∼
1.4.1.1.3 Sintering
The fi nal step in the production of a ceramic foam is the densifi cation of the green bodies by con-
ducting a high temperature sintering process. Foams are normally dried at room temperature for at
least 24 h prior to sintering. In this step, controlled heating is important to prevent collapse of the
ceramic network. The heating rate, sintering temperature, and holding time depend on the ceramic
starting materials. For example, values are in the range of 0.5-2°C/min, 1200-1350°C, and 2-5 h,
TABLE 1.10
Techniques of Direct Foaming and Direct Consolidation
Techniques
References
Direct foaming
1. Injection of gases through the fl uid medium
2. Mechanically agitating particulate suspension
3. Blowing agents
4. Evaporation of compounds
5. Evaporation of gas by
in situ
chemical reaction
20
Direct consolidation
1. Gelcasting
2. Direct coagulation consolidation (DCC)
3. Hydrolysis-assisted solidifi cation (HAS)
4. Freezing (quick set)
178
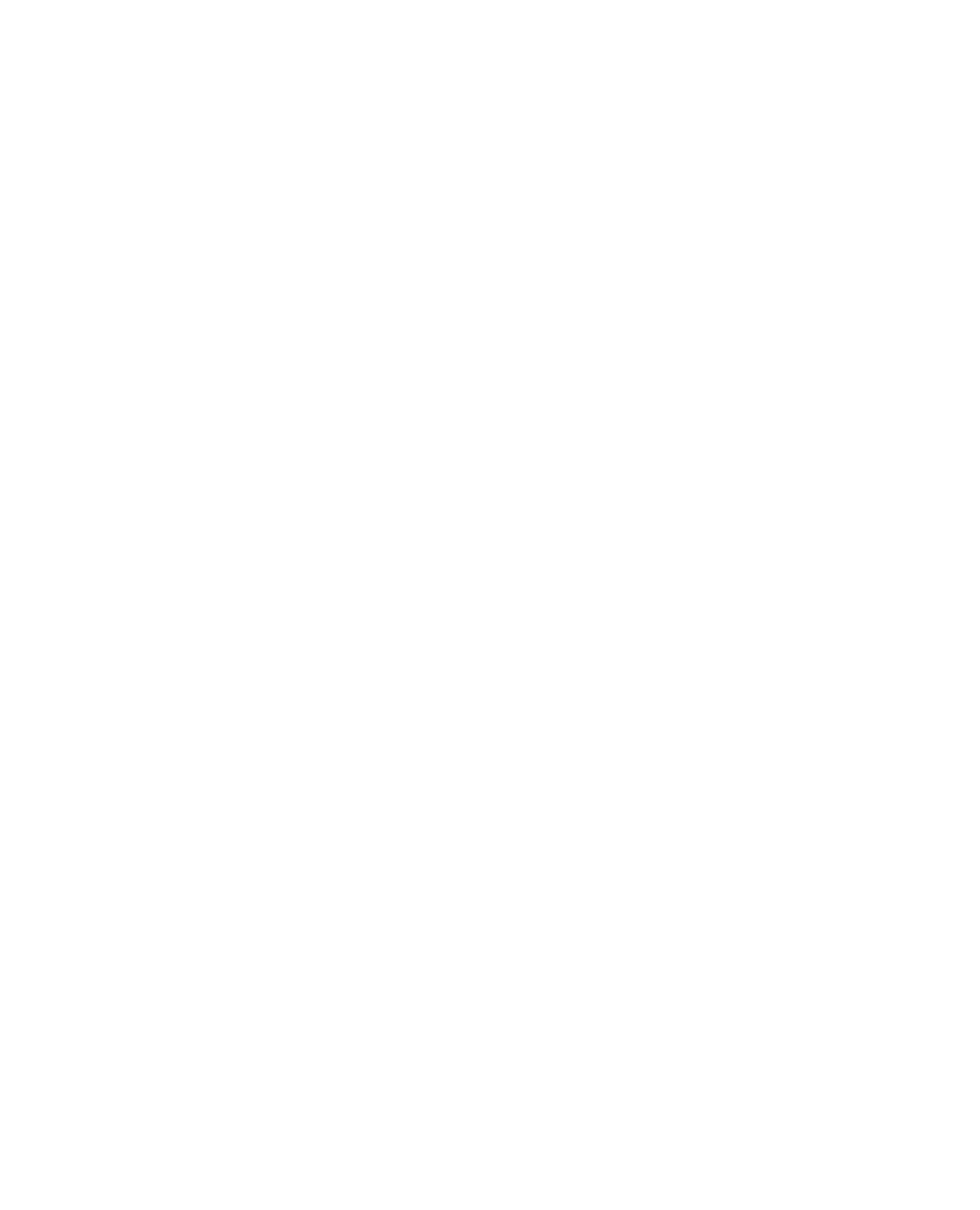
