Environmental Engineering Reference
In-Depth Information
ISG
EC
TC
VS
Battery
management
controller
I
S
G
Engine
Transmission
High voltage
ba
t
tery
Contactor
Figure 4.43 Hybrid vehicle electrical harness (courtesy Ford Motor Co.)
vehicle. A newly designed instrument cluster that provides additional information
to the driver and status of hybrid subsystems is integrated in the vehicle. A drive-
by-wire system, that is electronic throttle control, replaces the mechanical throttle
body (MTB).
The hybridization process adds several new components, such as a vacuum
pump, a cabin heat pump, a hybrid ac, an electric power assisted steering (EPAS), a
cooling pump for the respective controllers and a battery cooling fan. These com-
ponents are required in the vehicle to maintain production transparency of vehicle
functions during various modes of driving, such as engine shut off and vehicle run
condition as well normal engine run condition.
In the wiring architecture, identification of these new subsystems and com-
ponents and their electrical connectivity requirements is of prime importance. After
these have been identified, their location and packaging attributes will decide the
physical build of the harnesses - their branching and segmentation and the inter-
connections between them.
4.5.1 Cable requirements
Transition to a 42 V PowerNet vehicle electrical system will mean an overall
reduction in vehicle wiring harness mass and wire gauge. Figure 4.44 illustrates this
impact.
There will be a similar impact on vehicle electronic content as depicted in
Figure 4.45. The introduction of power electronics enabled functions will have a
concomitant increase in silicon content for the average passenger car. It should be
noted that control software in a vehicle electronic module represents some 30% of
the total module cost. In CY2000 about 4% of the vehicles value was in software.
By 2010 that number is estimated to reach 13% (Siemens VDO Automotive).




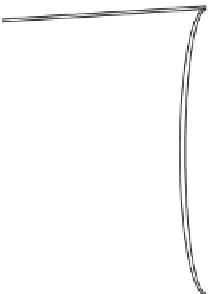

















































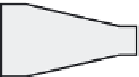






















































































