Biomedical Engineering Reference
In-Depth Information
In 2006, Yoon
et al
. studied the effect of additives such as glycerol, succinic acid, malic
acid, and tartaric acid on the physical properties of starch/PVA blend films; the results
showed that the flexibility and strength of the films could be improved with alcohol and
carboxylic acid functionalities.
Flieger and co-workers (2003), in their review, classify starch composites according to
their starch content: low (~10-20%), medium (~40-60%), and high amounts (~90%) of
starch, each class demonstrating distinct material properties. Addition of low amounts of starch
to, for example, polyethylene (Lim and Jane, 1992) accelerates the disintegration of the
polymer and the breaking apart of the material in such a way that the fast degradation of
starch produces pores in the remaining plastic film, which leads to a better interaction
between oxygen, microorganisms and the plastic molecules. In some applications photo
initiators, such as benzophenone derivatives, are used as pro-oxidants to speed up the
degradation progress
via
generation of free radicals, which results in polymer oxidation and,
finally, chain scission (Bagheri and Naimian, 2002).
Jansson and co-workers (2006) studied free films made of starch and PVA mixtures
(produced by casting) with respect to their mechanical and moisture uptake in order to
establish their potential as spray-dried powders. The moisture uptake was substantially
higher when glycerol was added and the glycerol-containing films had a lower failure
stress under tension than the corresponding glycerol-free films. Nevertheless, the films
containing 20% glycerol showed almost double the water uptake compared to the glycerol-
free films. The observed swelling behavior indicated that some of the powders were good
candidates for plastisol coatings, which are suspensions of polymer particles in a plasticizer
(Persico
et al
., 2009) (commonly dioptyl adipate) used mainly in textile inks.
Starch can also be chemically modified
via
esterification with fatty acids to synthesize
completely renewable and biodegradable materials. Sagar and Merrill (1995) esterified high
amylose starch with different chain length fatty acid chlorides in the presence of pyridine
and then evaluated the rheological, thermal, and mechanical properties of the resulting
materials. It was shown that ester groups within the structure act as internal plasticizers,
making the material more easily processable and more ductile. The starch esters of pentanoic
and hexanoic acid were semi-crystalline. The report showed that fatty acid modified starch
could be used for some applications where biodegradability is required but mechanical
property requirements are not too demanding. Moreover, it was shown that the degradation
rate of starch could be controlled by the degree of acetylation (Fringant
et al
., 1998 ).
A great deal of attention has been given to the incorporation of polysaccharides into
polyurethane (PU) foams (Donnelly
et al
., 1991). Attempts to form PUs from starch and its
degradation products, polyol glucoside ethers, suitable for polyurethane were reported in the
early 1960s (Otey and Miehltretter, 1962 ). Some methods for depolymerizing polysaccharides
are well known. For instance, starch can be enzymatically degraded to yield saccharide
mixtures (containing dextrin, maltose, maltotriose and glucose), high maltose syrups, or
high glucose syrups
via
the use of
-amylase, pullulanase, and amyloglucosidase enzymes
(Donnelly
et al
., 1991). Polyethers were derived from starch degradation products by
alkoxylation of the carbohydrate to a degree necessary to give a liquid of the desired viscosity
and hydroxyl number. Ge and co-workers (2000) utilized starch and wattle tannin of the
bark of
Acacia mearnsii
(a fast-growing tree native to Australia) and toluene diisocyanate to
synthesize flexible PU foams for car cushions, which need a high cross-linking density to
maintain a high-resilient property. On the other hand, Kim and co-workers (2007) used
starch as the main polyol component, with the amount of 30-50 wt-%, for polyurethane film
formation. Two endothermic peaks were observed by DSC analysis, resulting from urethane
α
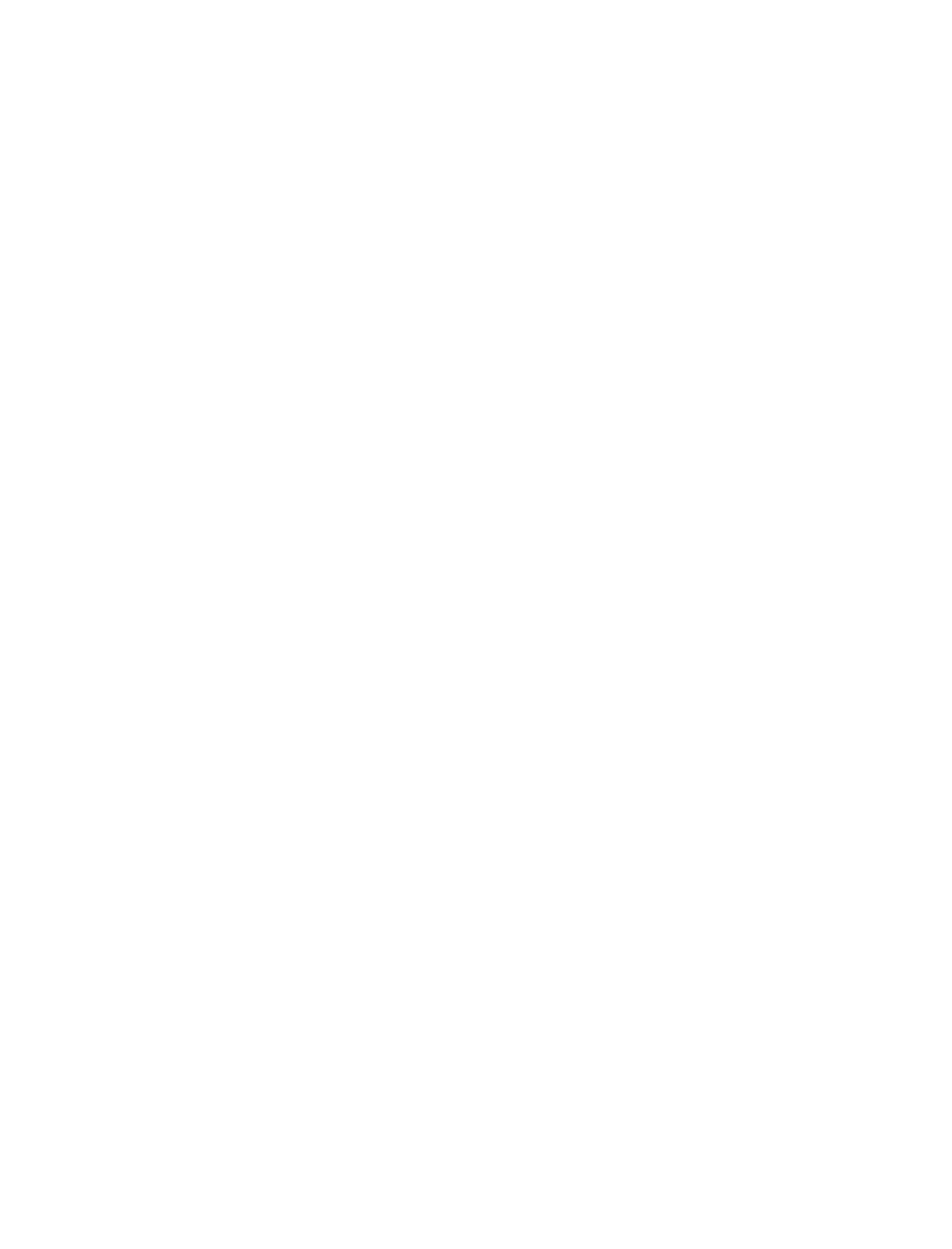



Search WWH ::

Custom Search