Graphics Reference
In-Depth Information
orates, and your final part will have a joint or
patch made only of ABS plastic.
Industrial Ring Habitat
Your exposure to acetone is greatest while
applying ABS glue and immediately after, so
pin your parts to a piece of cardboard or a
tray that you can immediately move to a
well-ventilated area away from your work-
space. If you move them outside, protect
them with a cardboard box to keep leaves,
dust, and grime out of the still-goopy slurry.
Artist Micah Ganske used ABS slurry glue to
assemble his groundbreaking sculpture Indus-
trial Ring Habitat from 1,000 3D-printed ABS
parts. He also uses it to glue PLA parts to ABS
—even though acetone doesn't dissolve PLA,
the slurry seeps into cracks and crevices to
mechanically bond the PLA parts to the ABS
base.
While acetone can “weld” the
edges of ABS parts to bond them,
this joint lacks the shear resistance
of parts printed together, because
the “melt zone” doesn't extend
deep into the surface. If an assem-
bly needs mechanical strength, de-
sign an interlocking joint with lots
of surface area—or use hardware.
Sanding 3D-Printed Plastic
Parts
When I first learned the basics of woodwork-
ing, I proved a lazy, inept sander of splintery
plywood toolboxes and lopsided Pinewood
Derby cars. My father suggested I forget
about “sanded” as a goal, and focus on “sand-
ing” as an activity. You cycle from coarse-grit
sizes down to finer-grit papers until the sur-
face is as smooth as you intend.
The same goes for sanding 3D-printed plas-
tics (
Figure 13-18
). With ABS and PLA, you
can work your way down to very fine papers
indeed—3M gem-polishing papers and
Micro-Mesh sanding tools with single-digit
micron grits that create scoring patterns in-
visible to the naked eye.
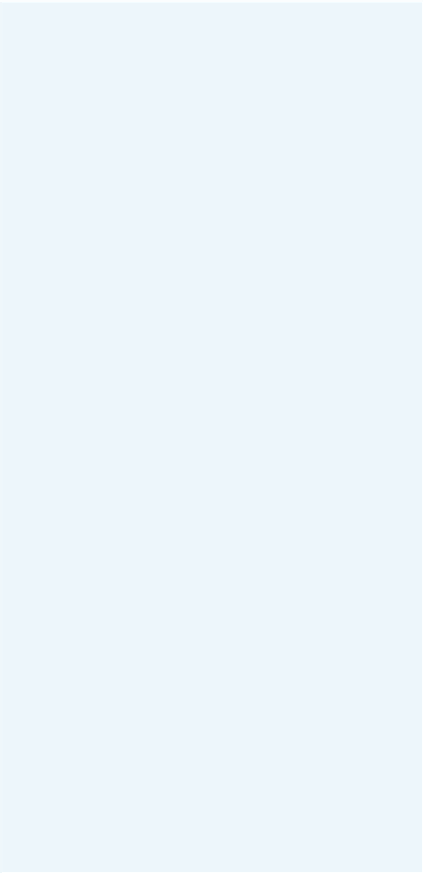








