Biomedical Engineering Reference
In-Depth Information
heart-valve applications, fine-grained isotropic graphite is
the most commonly used substrate. This substrate
graphite can be doped with tungsten in order to provide
radioopacity for X-ray visualizations of the implants. The
graphite substrate does not impart structural strength.
Rather, it provides a dimensionally stable platform for the
pyrolytic carbon coating both at the reaction temperature
and at room temperature.
Preform
Once the appropriate substrate material has been selec-
ted and prior to making a preform, it must be inspected
to ensure that the material meets the desired specifica-
tions. Typically, the strength and density of the starting
material are measured. Thermal expansion is ordinarily
validated and monitored through process control. The
preform, which is an undersized replica of the finished
component, is normally machined using conventional
machining methods. Because the fine-grained isotropic
graphite is very abrasive, standard machine tools have
given way to diamond-plated or single-point diamond
tools. In the case of heart valves, numerical control ma-
chining methods are often required to maintain critical
component dimensional tolerances. After the preform is
completed, it is inspected to ensure that its dimensions
fall within the specified tolerances and that it contains no
visible flaws or voids.
Fig. 3.2.11-7 Metallographic mount cross section of heat valve
component. The light-colored pyrolytic carbon layer is coated over
the interior, darker colored granular-appearing graphite substrate.
a metallographically prepared cross section of a pyrolytic
carbon component is shown in
Fig. 3.2.11-7
.
Machine to size
The components used to manufacture medical devices
have strict dimensional requirements. Because of the
inability, until recently, to precisely measure and control
bed size and indirectly coating thickness, the preforms
were generally coated more thickly than necessary to
ensure adequate pyrolytic carbon coating thickness on
the finished part. The strict dimensional requirements
were then achieved through precision grinding or other
machining operations. Because pyrolytic carbon is very
hard, conventional machine tools again cannot be used.
Diamond-plated grinding wheels and other diamond
tooling are required. The dimensions of final machined
parts are again verified.
Coating
Generally numerous preforms are coated in one furnace
run. A batch to be coated is made up of substrates from
a single lot of preforms. Such batch processing by lot is
required in order to maintain ''forward and backward''
traceability. In other words, ultimately it is necessary to
know all of the components that were prepared using
a specific material lot, given either the starting material
lot number (forward) or given the specific component
serial number (backward). The number of parts that can
be coated in one furnace run is dictated by the size of the
furnace and the size and weight of the parts to be coated.
The batch of substrates is placed within the fluidized bed
in the vertical tube furnace and is coated to the desired
thickness. Coating times are generally on the order of
a few hours, but the entire cycle (heat-up, coating, and
cool-down) may take as long as a full day.
A statistical sample from each coating lot is taken for
analysis. At this point, typical measurements include
coating thickness, microhardness and microstructure.
The microhardness, and microstructure are determined
from a metallo-graphically prepared cross section of the
coated component taken perpendicular to plane of de-
position. Thus, this test is destructive. An example of
Polish
The surface of as-deposited, machined and polished
components is shown in
Fig. 3.2.11-8
. It was found early
on in experiments (LaGrange
et al.,
1969; Haubold
et al.,
1981; Sawyer
et al.,
1975) that clean polished pyrolytic
carbon surfaces of tubes when placed within the vascu-
lature of experimental animals accumulated minimal if
any thrombus and certainly less than pyrolytic carbon
tubes with the as-deposited surface. Consequently, the
surfaces of pyrolytic carbon have historically been
polished, either manually or mechanically, using fine di-
amond or aluminum oxide pastes and slurries. The sur-
face finish achieved has roughness measured on the scale
of nanometers. As can be seen from
Table 3.2.11-2
(More
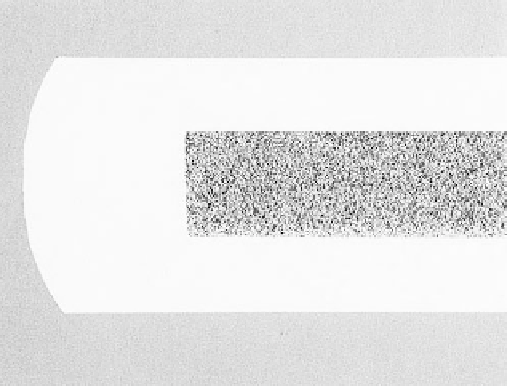







