Biomedical Engineering Reference
In-Depth Information
pyrolytic carbon material Weibull modulus is approxi-
mately 10 (More
et al.
, 1993).
Fracture toughness levels reflect the brittle nature of
the material, but the fluidized-bed isotropic pyrolytic
carbons are remarkably fatigue resistant. Recent fatigue
studies indicate the existence of a fatigue threshold that
is very nearly the single-cycle fracture strength (Gilpin
et al.
, 1993; Ma and Sines, 1996, 1999, 2000). Fatigue-
crack propagation studies indicate very high Paris-Law
fatigue exponents, on the order of 80, and display
clear evidence of a fatigue-crack propagation threshold
(Ritchie
et al.
, 1990; Beavan
et al.
, 1993; Cao, 1996).
Crystallographic mechanisms for fatigue-crack initia-
tion, as occur in metals, do not exist in the pyrolytic
carbons (Haubold
et al.
, 1981). In properly designed
and manufactured components, and in the absence of
externally induced damage, fatigue does not occur in
pyrolytic-carbon mechanical heart-valve components. In
the 30 years of clinical experience, there have been no
clear instances of fatigue failure. Few pyrolytic carbon
component fractures have occurred, less than 60 out of
more than 4 million implanted components (Haubold,
1994), and most are attributable to induced damage from
handling or cavitation (Kelpetko
et al.
, 1989; Kafesjian
et al.
, 1994).
Wear resistance of the fluidized-bed pyrolytic carbons is
excellent. The strength, stability, and durability of pyrolytic
carbon are responsible for the extension of mechanical-
valve lifetimes from less than 20 years to more than the
recipient's expected lifetime (Wieting, 1996; More and
Silver, 1990; Schoen, 1983; Schoen
et al.
, 1982).
Pyrolytic carbon in heart-valve prostheses is often
used in contact with metals, either as a carbon disk in
a metallic valve orifice or as a carbon orifice stiffened
with a metallic ring. Carbon falls with the noble metals in
the galvanic series (Haubold
et al.,
1981), the sequence
being silver, titanium, graphite, gold, and platinum.
Carbon can accelerate corrosion when coupled to less
noble metals
in vivo.
However, testing using mixed po-
tential corrosion theory and potentiostatic polarization
has determined that no detrimental effects occur when
carbon is coupled with titanium or cobalt-chrome alloys
(Griffin
et al.,
1983; Thompson
et al.
, 1979). Carbon
couples with stainless steel alloys are not recommended.
U.S. Food and Drug Administration GMP and Inter-
national Standards Organization ISO-9000 regulations.
As in the case of fabrication of metallic implants, nu-
merous steps are involved. Pyrolytic carbon is not ma-
chined from a block of material, as is the case with most
metallic implants, nor is it injection or reactive molded,
as are many polymeric devices. An overview of the
processing steps leading to a finished pyrolytic carbon
coated component for use in a medical device is shown in
Fig. 3.2.11-6
and is further described in the following
sections.
Substrate material
Since pyrolytic carbon is a coating, it must be deposited on
an appropriately shaped, preformed substrate (preform).
Because the pyrolysis process takes place at high tem-
peratures, the choice of substrates is severely limited.
Only a few of the refractory materials such as tantalum or
molybdenum/rhenium alloys and graphite can withstand
the conditions at which the pyrolytic carbon coating is
produced. Some refractory metals have been used in
heart-valve components; for example, Mo/Re preforms
were coated to make the struts for the Beall-Surgitool
mitral valve. It is important for the thermal expansion
characteristics of the substrate to closely match those of
the applied coating. Otherwise, upon cooling of the coated
part to room temperature the coating will be highly
stressed and can spontaneously crack. For contemporary
Steps in the fabrication of
pyrolic carbon components
Validate substrate
material
Machine preform
Caot preform
Machine to size
Steps in the fabrication of pyrolytic
carbon components
Polish
To convert a gaseous hydrocarbon into a shiny, polished
black component for use in the biological environment is
not a trivial undertaking. Furthermore, because of the
critical importance of long-term implants to a recipient's
health, all manufacturing operations are performed to
stringent levels of quality assurance under the auspices of
Assemble
Fig. 3.2.11-6 Schematic of manufacturing processing steps.
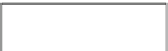

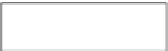

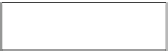

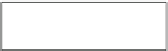

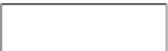













