Biomedical Engineering Reference
In-Depth Information
additions in the ternary alloy. That is, since Al is an alpha
(HCP) phase stabilizer while V is a beta (BCC) phase
stabilizer, it turns out that the Ti-6Al-4V alloy used for
implants is an alpha-beta alloy. The alloy's properties
depend on prior treatments.
O, grade 1), Ti 130 (0.125 wt.% O, grade 1), and Ti 160
(0.27 wt.% O, grade 3) was 88.3, 142, and 216 MPa, re-
spectively. Figure 3.2.9-11B shows similar results from
Turner and Roberts' (1968a) fatigue study on CP Ti
(tension-compression, 160 cycles/sec, mean stress
¼
zero) having a grain size in the range 26-32
m
m. Here the
fatigue limit for ''H. P. Ti'' (0.072 wt.% O, grade 1),Ti 120
(0.087 wt.% O, grade 1),and Ti 160 (0.32 wt.% O, grade
3) was 142, 172, and 295 MPa, respectivelydagain in-
creasing with increasing oxygen content. Also, for grade 4
Ti in the cold-worked state,
Steinemann
et al.
(1993)
reported a 10
7
endurance limit of 430 MPa.
Figure 3.2.9-11C, from
Conrad
et al.
(1973)
,sum-
marizes data from several fatigue studies on CP Ti at
300K. Note that the ratio of fatigue limit to yield stress is
relatively constant at about 0.65, independent of in-
terstitial content and grain size. Conrad
et al.
suggest that
this provides evidence that ''the high cycle fatigue
strength is controlled by the same dislocation mechanisms
as the flow [yield] stress'' (p. 996). The work of Turner
and Roberts also reported that the ratio
f
(fatigue limit/
ultimate
Microstructure and properties
ASTM F67
For relatively pure titanium implants, as exemplified by
many current dental implants, typical microstructures
are single-phase alpha (HCP), showing evidence of mild
(30%) cold work and grain diameters in the range of 10-
150
m
m(
Fig. 3.2.9-10
), depending on manufacturing.
The nominal mechanical properties are listed in
Table
3.2.9-2
. Interstitial elements (O, C, N) in both pure ti-
tanium and the Ti-6Al-4V alloy strengthen the metal
through interstitial solid solution strengthening mecha-
nisms, with nitrogen having approximately twice the
hardening effect (per atom) of either carbon or oxygen.
As noted, it is clear that the oxygen content of CP Ti
(and the interstitial content generally) will affect its yield
and its tensile and fatigue strengths significantly. For
example, data available in the ASTM standard show that
at 0.18% oxygen (grade 1), the yield strength is about
170 MPa, whereas at 0.40% (grade 4) the yield strength
is about 485 MPa. Likewise, the ASTM standard shows
that the tensile strength increases with oxygen content.
The literature establishes that the fatigue limit of
unalloyed CP Ti is typically increased by interstitial con-
tent, in particular the oxygen content. For example,
Fig. 3.2.9-11
A shows data from
Beevers and Robinson
(1969)
, who tested vacuum-annealed CP Ti having a grain
size in the range 200-300
m
m in tension-compression at
a mean stress of zero, at 100 cycles/sec. The 10
7
cycle
endurance limit, or fatigue limit, for Ti 115 (0.085 wt.%
which is also called the
''fatigue ratio'' in materials design textbooks (e.g.,
Charles
and Crane, 1989
, p. 106)
tensile
strength)
d
was 0.43 for the high-purity
Ti (0.072 wt.% O), 0.50 for Ti 120 (0.087 wt.% O), and
0.53 for Ti 160 (0.32 wt.% O). It seems clear that in-
terstitial content affects the yield and tensile and fatigue
strengths in CP Ti.
Also, cold work appears to increase the fatigue prop-
erties of CP Ti. For example,
Disegi (1990)
quoted
bending fatigue data from for annealed versus cold-
worked CP Ti in the form of unnotched 1.0 mm-thick
sheet (
Table 3.2.9-5
); there was a moderate increase in
UTS and ''plane bending fatigue strength'' when compar-
ing annealed versus cold-rolled Ti samples. In these data,
the ratio of fatigue strength to ultimate tensile strength
(''endurance ratio'' or ''fatigue ratio'', see paragraph above)
varied between 0.45 and 0.66. Whereas the ASM
Metals
Handbook
(
Wagner, 1996
) noted that the fatigue limit for
high-purity Ti was only about 10% larger for cold-worked
versus annealed material, Desegi's data shows that the
fatigue strength increased by about 28%, on average.
In recent years there has been increasing interest in
the chemical and physical nature of the oxide on the
surface of titanium and its 6Al-4V alloy and its biological
significance. The nominal composition of the oxide is
TiO
2
for both metals, although there is some disagree-
ment about exact oxide chemistry in pure versus alloyed
Ti. Although there is no dispute that the oxide provides
corrosion resistance, there is some controversy about
exactly how it influences the biological performance of
titanium at molecular and tissue levels, as suggested in
literature on osseointegrated oral and maxillofacial im-
plants by Br
˚
nemark and co-workers in Sweden (e.g.,
Kasemo and Lausmaa, 1988
).
d
Fig. 3.2.9-10 Microstructure of moderately cold-worked
commercial purity titanium, ASTM F67, used in an oral implant.
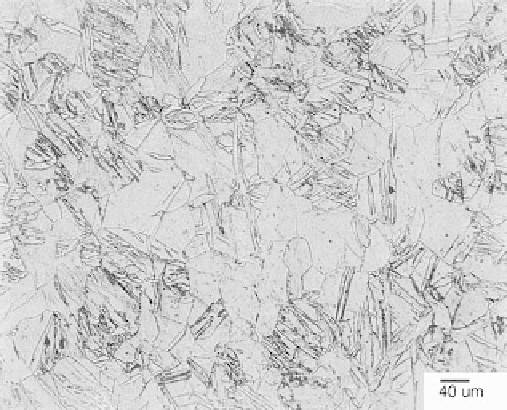



