Geology Reference
In-Depth Information
As noted earlier, opening and closing of the (rotating) rotor relative to the
(stationary) stator in the presence of mud flow introduces a periodic water
hammer disturbance into the drilling channel. Constant rotation speeds produce
purely periodic signals without information content. Rapid changes to rotation
speed are important to high speed telemetry, and these must be accompanied by
low resistive torque, high “delta-p” ( p) signal strength, low erosion (difficult to
achieve because small rotor-stator gaps are required for large amplitudes), good
acoustic efficiency (that is, sound energy is desired in the primary but not higher
harmonics), and so on. We have relied on both experimental and theoretical
methods to optimize high-data-rate mud pulse designs.
The signal generation process itself depends strongly on a highly three-
dimensional process with significant hydraulic-acoustic interaction. This is
difficult to model, either analytically or computationally. Thus, our principal
approach has been to model signal generation and erosion using rapid, cost and
time-effective wind tunnel analysis and subsequently rescaling results to actual
mud weight and flow rate conditions later. In Figure 5.11, we show a mud siren
mounted within the test section of a “short wind tunnel” designed and used at
CNPC with these special objectives in mind. Additional instruments, not
shown, monitor torque, angular position and erosion tendencies during rotation.
Figure 5.11.
Siren test sections with “differential transducers” for signal
strength measurement (not influenced by reflections and propagating noise).
Figure 5.12.
Short wind tunnel, “bird' s eye” perspective.

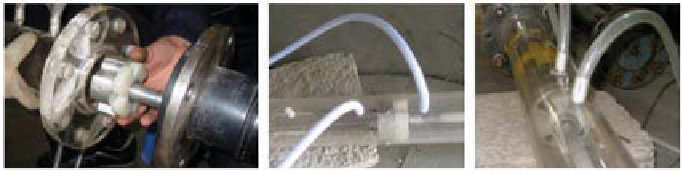









Search WWH ::

Custom Search