Biomedical Engineering Reference
In-Depth Information
200 nm
FIGURE 5.25
SEM micrograph of nanocrystalline titania coating fabricated sol-gel-derived coating after annealing at 550°C.
(From Biju, K.P., Jain, M.K.,
Thin Solid Films
, 516, 2175-2180, 2008. With permission.)
Physical Vapor Deposition
Physical vapor deposition (PVD) is a powerful technique to fabricate hydrophilic nano-
TiO
2
coatings. Magnetron sputtering offers uniform deposition and precise control of the
deposition rate. High quality of nanocrystalline TiO
2
coatings can be produced by careful
control of the processing parameters. As reported by Ye et al. (2007), a TiO
2
target is used
and annealing can transform the amorphous titania into a crystalline coating. However,
a low heating rate can prevent film cracking. As shown in Figures 5.26 and 5.27, the water
contact angle is progressively influenced by the treatment temperature. The mean diam-
eter of the grain is about 30 nm. The annealing temperature influences the final grain size.
Generally, a higher temperature induces a larger grain size and the contact angle drops, but
from about 600°C the contact angle is nearly independent of the processing temperature.
A pure Ti target can also be used as the target and a mixture of Ar and O
2
serves as the
working gas (Yang et al. 2008b). The deposition rate is about 70 nm/h and the mean grain
size around 40 nm. Subsequent annealing enlarges the grain size. Cell adhesion measure-
ment shows that the longer heating time enhances cell adhesion and a heat treatment for
3 h increases the ALP activity of the cells. The nanoscaled coating significantly improves
241207
SEI 15.0 kV ×75,000
100 nm
WD 16 mm
FIGURE 5.26
Surface morphology of TiO
2
thin film prepared by RF magnetron sputtering with annealing treatment at 200°C.
(From Ye et al.,
Vacuum
, 81, 627-631, 2007. With permission.)
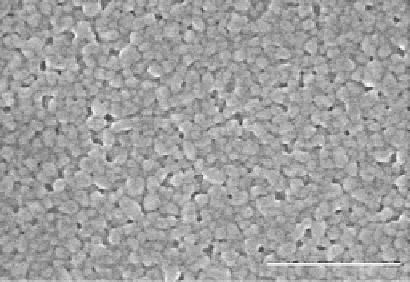
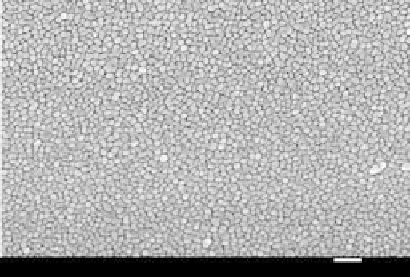
Search WWH ::

Custom Search