Environmental Engineering Reference
In-Depth Information
Solid input
Zone 1
Zone 2
Die
Plasticizer
Additives
Figure 6.24
Twin-screw extruder configuration for the transformation of raw agricultural
products.
Starch granules "melting" and
ligno-cellulosic fibres defibration
Cell wall break
Figure 6.25
Transformations taking place in the twin-screw extruder.
The transformation of sunflower oilcake is similar. The globulin corpuscles are
denatured in low moisture conditions to form a continuous matrix. The real differ-
ence lies in the structure of the peptide chains compared to starch. Many different
interactions take place between the proteins, and their texturation does not result
in a simple 'thermoplastic' flow as occurs for starch.
Sugar beet pulp is made of primary cell walls. The breakage of the structure has
to be performed at a smaller scale, and greater energy is needed to break some of the
covalent bonds between the cell wall polysaccharides. The use of the die is therefore
necessary to increase the residency time in the extruder. The final structure consists
of cellulose micro-fibres embedded in a pectin and hemicelluloses matrix.
Injection moulding is the first targeted forming technology for agromaterials.
Without any complex technological modification, injection-moulded objects can be
obtained quickly and easily. At the end of the twin-screw extrusion process, the
obtained granulates are stable and mouldable by injection. The French company
Vegeplast is the world leader of this technology. Typically, the shaped materials are
dense (density c. 1.4 kg m
-3
), relatively stiff and brittle (flexural modulus c. 4 GPa;
strength at break c. 17 MPa), and water sensitive. The latter is a profitable
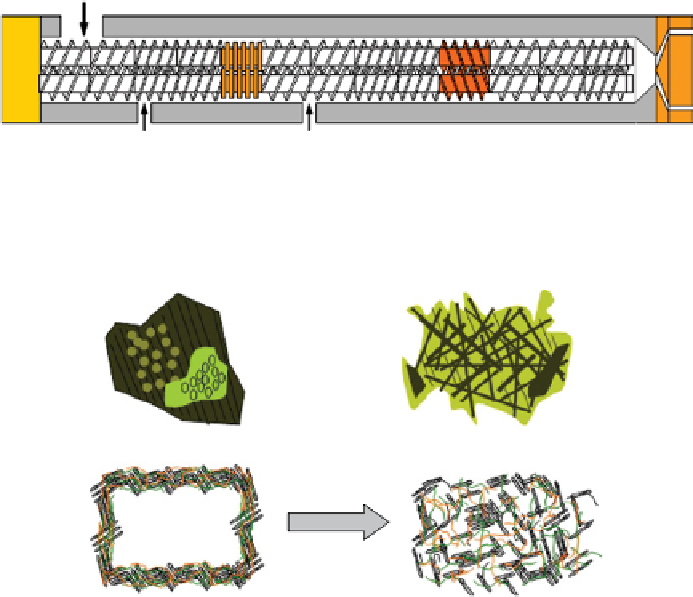
