Environmental Engineering Reference
In-Depth Information
Airfoils designed for the root and tip sections must not only address local aerodynamic
requirements, but it is also desirable that they produce a monotonic change in aerodynamic
properties from root to tip and a “faired” blade surface. The root section should be thicker
for structural reasons, and it can accept a higher
C
L,max
.
The tip section needs to be thinner,
with lower values of both minimum drag and
C
L,max
.
Two airfoil shapes shown in Figure
6-7, the
SERI S807
and
S806A
,
have been designed for the root (
r/R
» 0.40) and tip (
r/R
» 0.95) regions, respectively, to meet these requirements.
HAWT Rotors 21 m to 35 m in Diameter
It should be noted that designing airfoils specifically for wind turbines may obtain
benefits not only by improved aerodynamic performance but also by improved structural
performance and lower blade costs. The thickness-to-chord ratio of an airfoil plays a very
significant role in its strength and stiffness, and this is particularly important for longer
HAWT blades. For this reason, a family of thicker airfoils has been designed for rotors
from 21 to 35 m in diameter, on lines similar to those of the SERI S805A/806A/807 family,
with the designations
S812, S813,
and
S814
(Fig. 6-8). The thickness-to-chord ratio of the
S812 is 0.210, compared to 0.135 for the S805A. Wind tunnel tests confirm that these
thicker airfoils also have a limited
C
L,max
(in the range of 1.00) which is insensitive to
surface roughness, and low drag. The latter is accomplished by maintaining large areas of
laminar flow.
Figure 6-9 shows a third set of airfoils designed for HAWTs with diameters of 36 m
and larger, tailored for an optimum combination of aerodynamic performance and strength.
These are designated as
S816, S817
,
and
S818
airfoils.
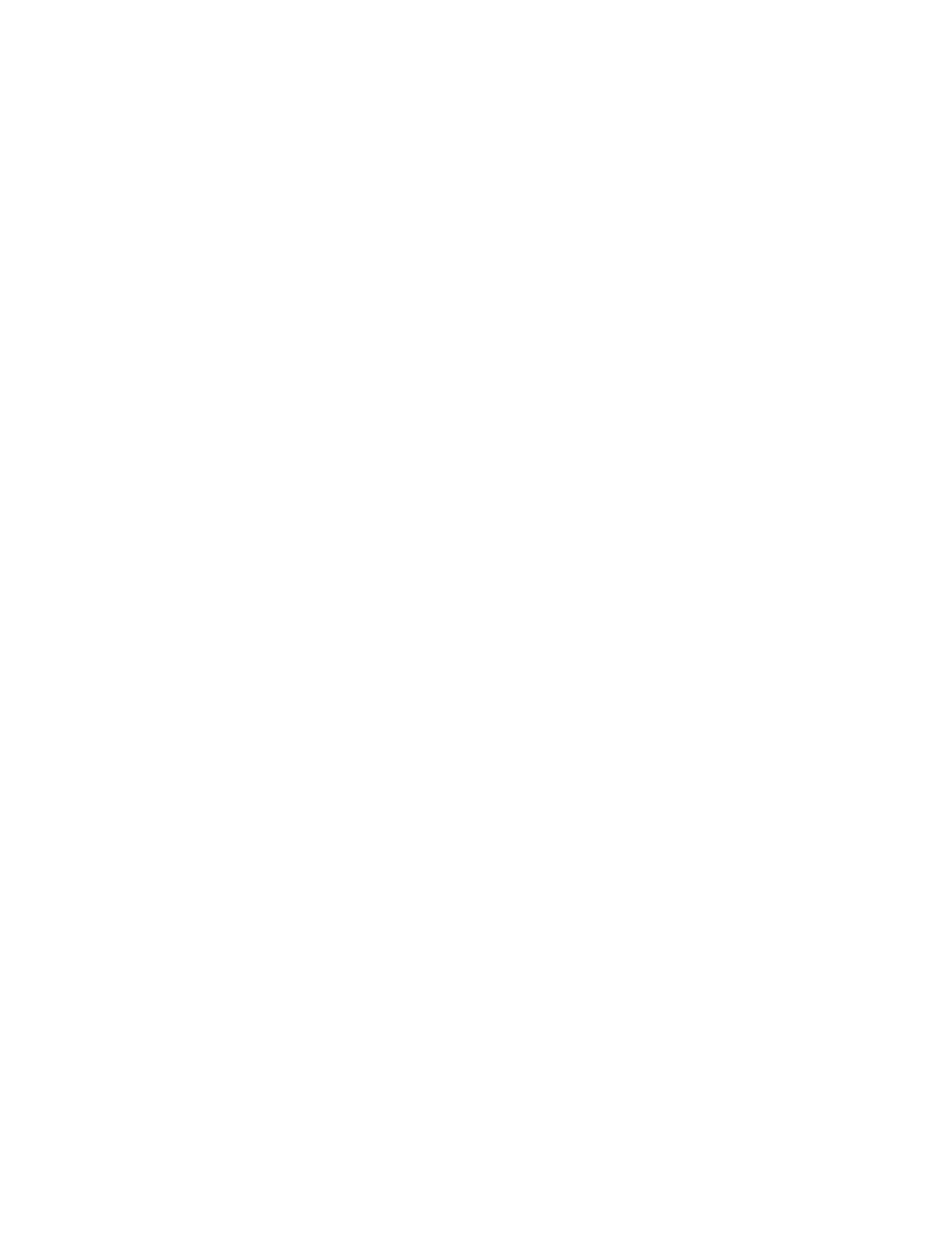
Search WWH ::

Custom Search