Environmental Engineering Reference
In-Depth Information
we make our membrane more selective we can get by with using a
smaller membrane. To understand this result we have to realize that in
our membrane the pressures at the permeate and feed are fi xed. The
pressure ratio limit requires that the maximum CO
2
concentration in the
feed be 50%. Hence, the remainder must be N
2
. All these nitrogen mol-
ecules need to pass the membrane! The fact that we need to obey the
mass balance implies that if we decrease the permeability of our mem-
brane for nitrogen, we have to make a much larger membrane to keep up
with the fl ux of nitrogen.
With this background information, we can now better understand
that there exists an optimal selectivity. If we increase the selectivity, the
concentration of CO
2
in our permeate increases. However, once we have
reached a selectivity above 100, we see that a further increase of
the selectivity by, say, a factor of two, has only a very small effect on the
concentration of CO
2
in our permeate, but does increase the membrane
area by almost a factor of two. The shaded area in
Figure 7.3.2
gives
the range for which we have an optimal separation.
Making membranes
The manufacture of industrial scale membrane separation units is a
mature industry. Asymmetric hollow fi ber membranes are one common
design in industries such as dialysis and water purifi cation. The ideal
membrane unit has a high selectivity and a high permeability with as thin
a membrane as is physically possible. However, such an extremely thin
membrane can be fragile. The main idea of an asymmetric membrane is
to deposit the active membrane material on a support that distributes the
mechanical stresses associated with the operation. The support itself is
often a polymer with a porous microstructure that affords little resistance
to gas or fl uid fl ow, yet gives the active membrane mechanical stability.
The resulting membrane construct is what we call an asymmetric mem-
brane (see
Figure 7.3.3
) [7.2].
The other attribute of membrane separations is the ability to create a
very large surface area with a compact device. The technology that has
been developed to achieve this uses a technique in which one simultane-
ously co-extrudes the selective layer and the support layer. With this
co-extrusion process, one can create hollow fi bers. These fi bers can be
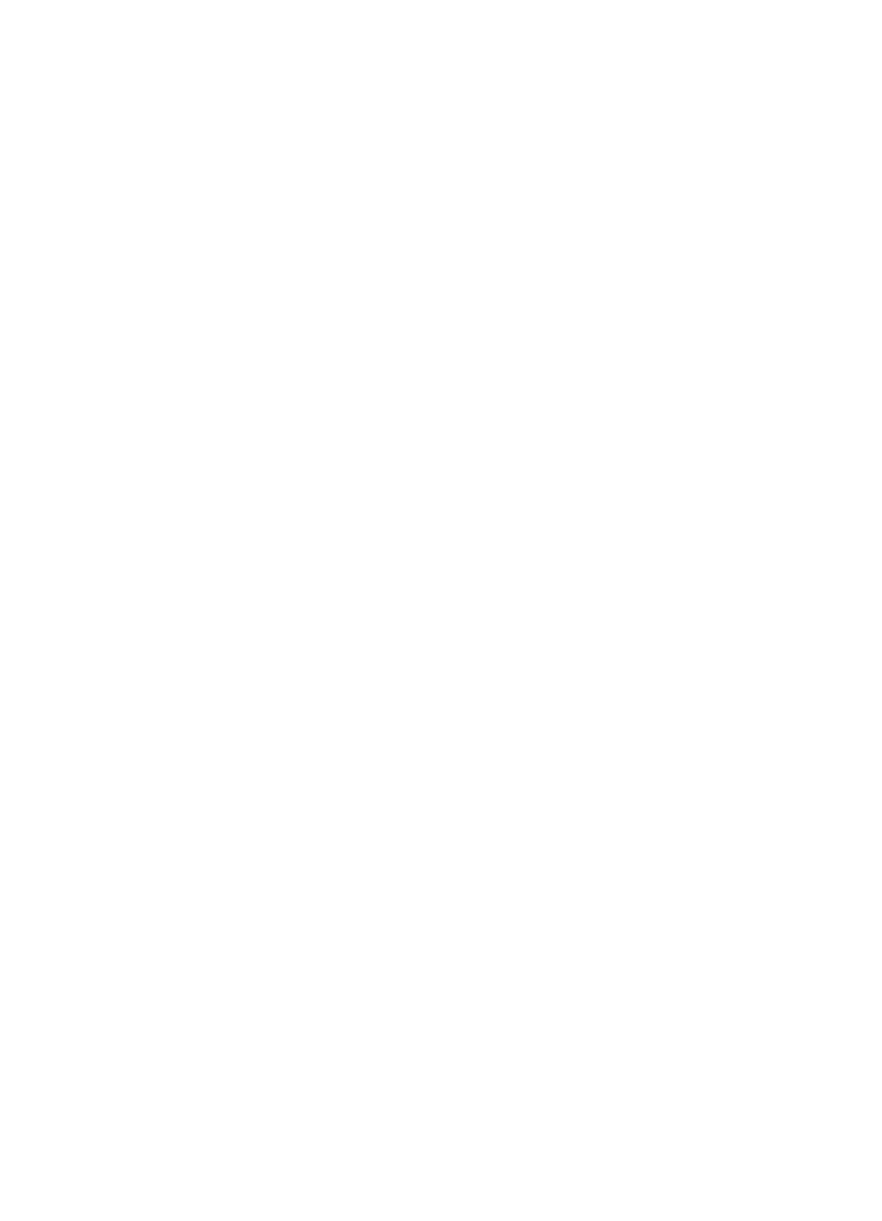



Search WWH ::

Custom Search