Environmental Engineering Reference
In-Depth Information
Figure 9.6: Effect of Mo content of catalysts reprocessed from coked spent cata2lysts (a: catalyst
A; b: catalyst B; c: catalyst C) on hydrodevanadization (HDV) and hydrodenickelization (HDNi)
activities at 370 and 390
C [From ref.
522
. Reprinted with permission].
Al
2
O
3
together with carbonaceous deposits. The spent catalyst was mixed with an alumina
containing material and extruded to prepare the new catalysts. The prepared catalysts
contained 1.7 wt.% Mo, 0.6 wt.% Co and had a higher percentage of pores in the 60-500 A
range. High temperature calcination (at 800
◦
C) was used for pore enlargement in the catalyst.
The catalyst was found to be very effective for HDM residual feeds. In another related study,
de Boer
[528]
used a decoked spent CoMo/Al
2
O
3
HDS catalyst that contained high levels of
MoO
3
(20 wt.%) and CoO (5 wt.%) and small amount of V
2
O
5
(0.2 wt.%) and NiO (0.1 wt.%)
for preparing a large pore hydroprocessing catalyst. The spent catalyst was mixed with
alumina in the form of a fine powder (particle size
<
20
m) and extruded to produce new
catalyst extrudates. The prepared catalyst contained 13 wt.% MoO
3
and 3.2 wt.% CoO on
alumina support. High temperature calcination treatment was used for pore enlargement. A
sample of the catalyst that was calcined at 750
◦
C had large pores with mean pore diameter of
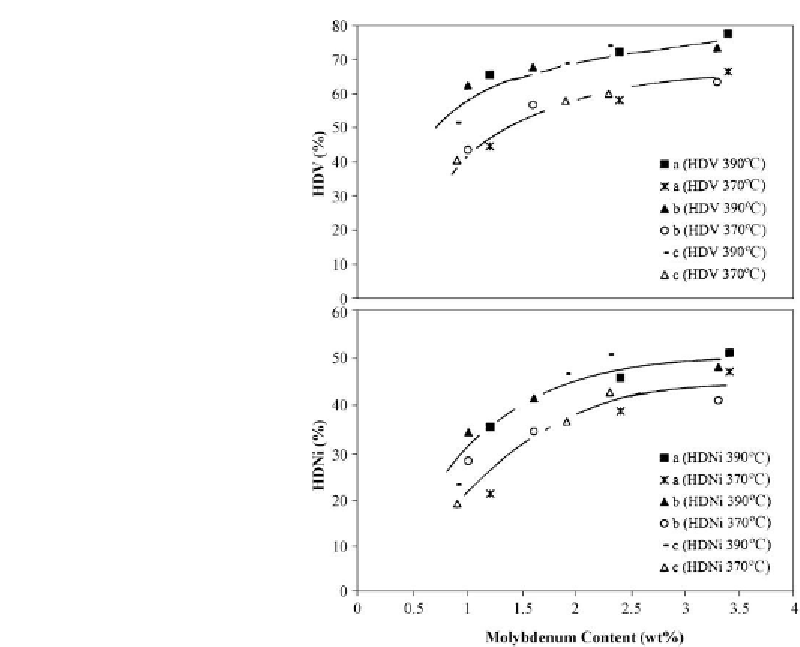






