Environmental Engineering Reference
In-Depth Information
Fig. 3 The relationship
between the various film
thicknesses of the
P3HT:PC
61
BM layer and the
blade speeds
1.3 Coating Instabilities
In typical roll-to-roll coating process such as gravure coating, the surface of the
printing rolls has many engraved cells. A picture of the gravure coating system is
shown in Fig.
8
. The ink in the engraved cell on the roll surface is transferred to
substrate in the roll-to-roll coating, while there is direct contact between the
gravure roll and the substrate (in comparison with blade or die coating where a
fluid layer exists between the two rolls, and later will be referred as non-contact
coating process). The direct contact mechanism of the ink transfer causes printing/
coating instability, such as in the form of streak patterns in the film as shown in
Fig.
6
. The small amount of the ink in the gravure cell moves like an extensional
viscous flow during the ink transfer. The extended viscous fluid causes irregular
streak patterns. An example is shown in Fig.
4
for the emissive polymer solution/
material. This coating instability can be explained by the capillary number, C
a
.
This dimensionless number is defined by the surface energy and viscosity of the
solution.
C
a
¼
lV
r
ð
8
Þ
l: the viscosity of fluid, V : the flow rate (roll speed), r: the surface tension.
Typically, larger C
a
will cause coating instabilities, such as ribbing, cascading, and
coating mist, due to the cavitation.
The viscosity of the solution increases for higher molecular weight material.
For instance, the emissive polymer in the light-emitting diodes has relatively high
molecular weight around 1,000,000. Therefore, the coating problem can be more
severe. Generally, viscosity also increases with the solution concentration, which
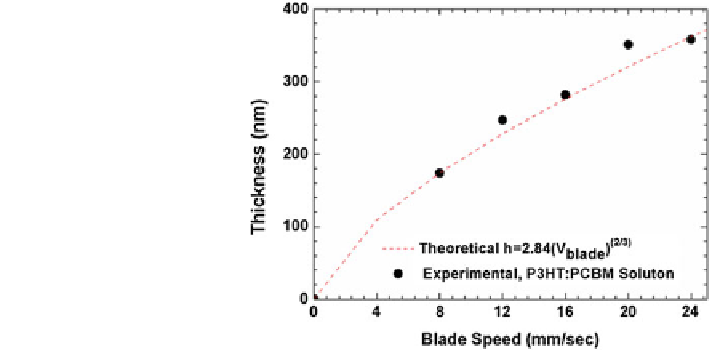
Search WWH ::

Custom Search