Hardware Reference
In-Depth Information
Figure 3.72: Configuration of parallel structure.
PID-type Controllers for Parallel Structure
PID type controllers are the most commonly found in practice. As the first
example, we consider PID controller for both VCM and microactuator. As
elaborated in the following design, this approach gives a stable system although
some aspects of hand-off are not so desirable.
VCM Control ler
Let us assume that the VCM resonance is compensated using a notch filter
so that the compensated model can be regarded as a double integrator k/s
2
.
Let the desirable crossover frequency for the VCM actuator be f
V
. Then the
lag-lead compensator is:
C
VP
(s)=k
c
(1/ω
2
s +1)
(1/ω
1
s +1)
(1/ω
3
s +1)
(1/ω
4
s +1)
,
(3.149)
with ω
2
higher than ω
1
by a factor 5, ω
4
higher than ω
3
by a factor of 5 or
more, and f
V
higher than ω
3
by a factor of 2-3 or more but lower than ω
4
by
a factor of 2-3 or more. As discussed in the case of single stage actuator, such
a scheme can give us a lag-lead compensator for the double integrator type
plant with 35
◦
or more phase margin and minimum of 6 dB gain margin.
Microactuator Controller
Let the microactuator gain be g
m
and the microactuator loop crossover
frequency be f
m
. Obviously f
m
should be a few order of magnitude higher than
f
V
as the microactuator is expected to respond to high frequency components
of PES. We use a lag filter with the corner frequency of 1/β (e.g. 1/4) of f
m
:
1
C
m
= k
m
2πf
m
s +1
,
(3.150)
β
with |g
m
C
m
(s)|
s=j2πf
m
= 1, such that the microactuator loop crosses 0-dB
line with -20 dB/dec slope.
Since the microactuator loop works in parallel with the VCM loop which
has a -60 dB, -40 dB, -20 dB and -40 dB/dec slope, the low frequency gain
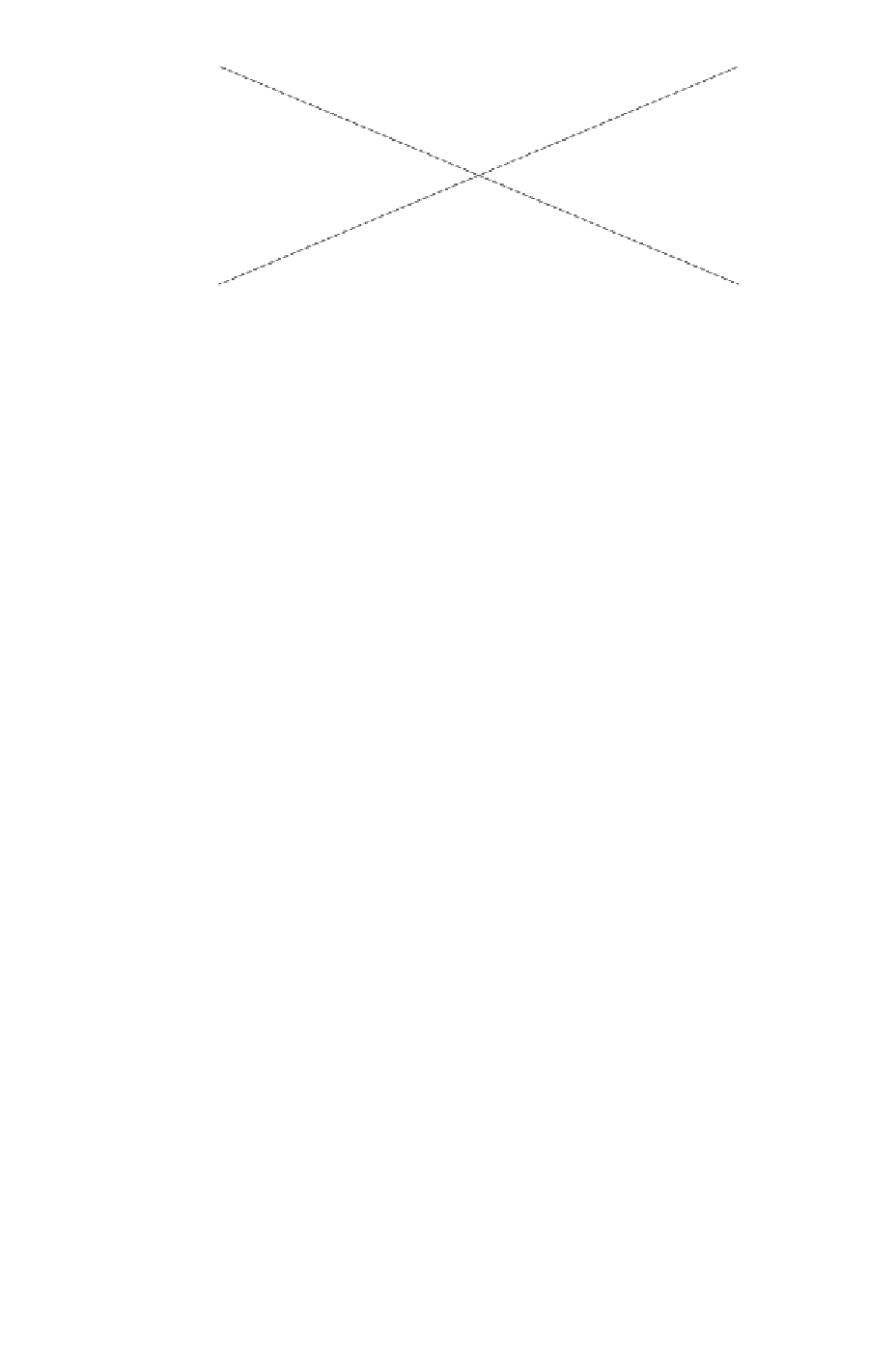

