Biomedical Engineering Reference
In-Depth Information
FIgure 20.3
CAD model of Straumann Standard Plus Implant used in the simulations.
with an 8° Morse taper abutment-to-implant connection with an internal octagon (Figure 20.3). The
dental implant was manufactured in commercially pure titanium. A porcelain-fused-to-metal (PFM)
crown with gold alloy was employed. In order to ensure accurate representation, the three-dimensional
models of the bracket, arch wire, and dental implants were assessed by a clinical dentist.
The FE models were meshed using 10-node solid tetrahedral elements in ANSYS software
(Swanson Analysis System Co., Houston, TX). To check for model convergence, models were cre-
ated with element sizes of 0.5, 1, 1.5, 2, and 2.5 mm. For each model, the total strain energy was
calculated and compared under the same loading and boundary conditions. The total strain energy
was reduced by 1.7% with each increase in element size from 0.5 to 1 mm and further reduced
by 5.3% with each increase from 1 to 1.5 mm. With elements from 1.5 to 2 mm and 2 to 2.5 mm,
strain energy decreased 13.2% and 16.8%, respectively. The computing time for the 0.5 mm model
was 20 minutes, but it was substantially reduced to 8 minutes for the 1 mm model. As shown in
Figure 20.4, a 1-mm-per-element size was adopted.
20.2.2 m
ecHanoreGulation
B
one
r
emodelinG
a
lGoritHmS
According to different clinical problems, different mechanoregulation bone remodeling algorithms
were developed and implemented into the FE model.
1.
Tooth movement algorithms incorporating both external and internal remodeling mecha-
nisms
. The algorithms were divided into external and internal remodeling components.
An external remodeling principle was employed to predict tooth movement, keeping
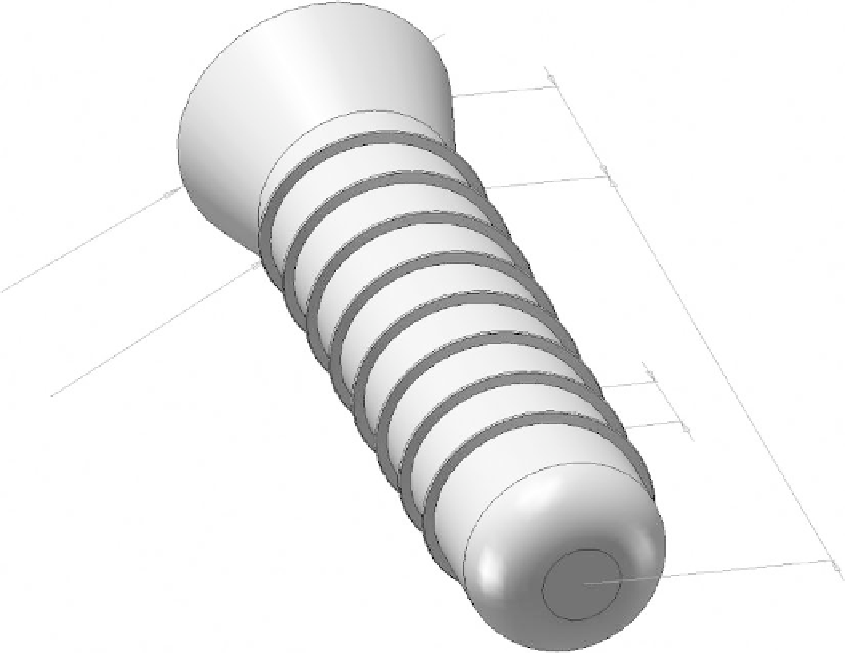
Search WWH ::

Custom Search