Civil Engineering Reference
In-Depth Information
Fig. 4.25
Magnesium surface of stress ratio as a function of instantaneous current and true strain
model is that it does not fully encompass the notion that the addition of electricity
lowers the yield point of the material. This is most prevalently seen in the Copper
C11000, where error is a maximum directly after yield. This error is more pro-
nounced in the Copper C11000 as compared to the magnesium, as the applica-
tion of electricity significantly decreased the yield point of the copper compared to
magnesium. Another aspect that should be considered to improve this model is the
field density throughout the specimen, thus possibly using barreling compensation
and incorporating frictional affects (especially for larger strains). An added factor
that may also play a crucial role in modeling the flow stress is the occurrence of
an electrical threshold [
2
]. This threshold causes a non-uniform stress distribution
between current densities for a given strain.
4.5.1.5 Conclusion for Non-constant Current
Density Empirical Modeling
This section developed an initial empirical relationship, which provided a rep-
resentation for the flow stress during an EAM compression test across different
materials. The preliminary results from this study show positive results for the
classification of flow stress over short and larger ranges of strain. Also, the results
obtained from this study have allowed review of the many aspects that affect the
flow stress in relation to the addition of electrical current.
4.5.2 Constant Current Density
Considering a model that would be capable of mapping the flows stress for an
electrically assisted forming process is highly useful for process planning and
parameter selection. The previous section presented an empirical model for
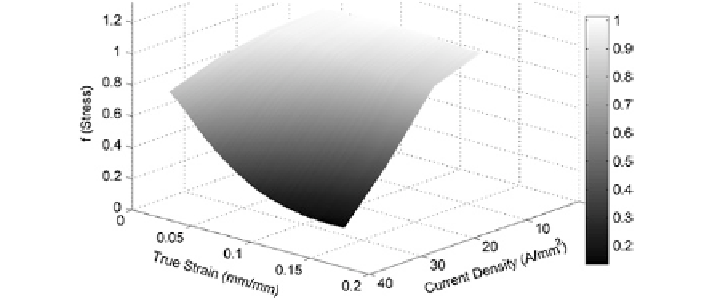