Civil Engineering Reference
In-Depth Information
11.4.1 Compression
Explanations of two key EAM compression works will be discussed. In the first
work, EAM compression tests will be run on various types of metals, and using
several size specimens [
8
]. The second research work focuses on the impact that
manufacturing speed has on Mg compression specimens [
17
].
11.4.1.1 EAM Compression Results on Various Metals
In the work by Perkins et al., EAM compression tests were run on various types of
metal alloys, including aluminum alloys (Al6061-T6511, Al7075-T6, Al2024-T4,
Al2024-T351), copper-based alloys (C11000, 360 brass, 464 brass), ferrous-based
alloys (304 Stainless Steel, A2 steel), and titanium alloy [
8
]. In addition, this work
explored two different specimen sizes for several of the metals mentioned above.
The specimens were compressed 6.4 mm (a 60 % height reduction) with a platen
speed of 25.4 mm/min, while various starting current densities were applied to
the specimens constantly throughout each test. Figure
11.35
shows stress-strain
curves for the titanium alloy at different starting current densities. From this work,
an “electrical threshold” effect was discovered. Specifically, there is a particular
current density in which a significant reduction in forming load is witnessed, or a
significant improvement in formability is observed.
Conclusions from this work are as follows:
• There is an “electrical threshold” where electroplastic effects are produced, which
is specific to each material.
• The electrical threshold is a function of the starting current density, die speed,
and material.
Fig. 11.35
Electrical threshold effect (Ti-G5) [
8
]. Once a particular current density level is
reached, which is specific to each metal alloy, a significant force/stress reduction due to EAM
will take place. This current density level is denoted as the “electrical threshold” level at the par-
ticular electrical settings
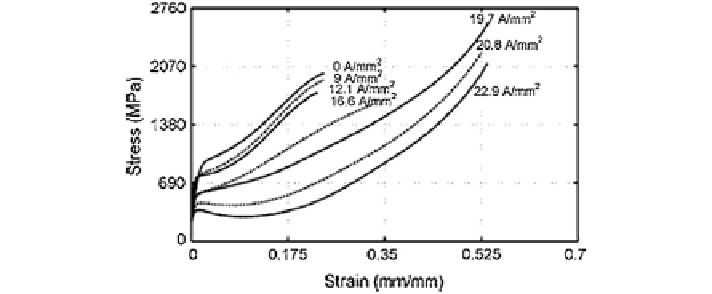