Civil Engineering Reference
In-Depth Information
Fig. 11.34
Cross section of welded specimen with (
left
) start of the weld and (
right
) middle of
the weld [
16
]
11.3.4 Conclusions and Future Work
This work showed the first experimental modification of the welding feed force and
torque during the process of EAFSW. As a result, these preliminary results show
great potential for improved welding speed and penetration depth. Additionally,
these results suggest the possibility of reduced tool wear during plunging and weld-
ing due to enhanced material softening. Also, as the application of current is capa-
ble of reducing the material strength, significantly stronger or thicker materials may
be welded with the EAFSW process where they are prohibited by traditional FSW.
Moreover, with the reduction in forces (on average 58 %) and torque at the begin-
ning of the weld, smaller capacity machines could be used or adapted to perform
FSW with electrical assistance. This could reduce the capital cost for manufactures
that use this type of welding process.
Further work is examining the interactions of processing conditions, tool geom-
etry, and electric current magnitude on the material flow and heat generation during
the welding process. Also, the microstructure evolution during the process should be
analyzed to compare the traditional FSW process to the EAFSW process.
11.4 Experimental Findings for Alternative EAF Processes
Throughout the last decade, many works have been published which experimen-
tally examine the effect of EAM on different processes. In the following sections,
experimental works involving EAM's impact on uniaxial compression, uniaxial
tension, non-uniform deformation, and springback will be discussed. Included in
these discussions will be examples of work by the authors, as well as work by
other EAM researchers.
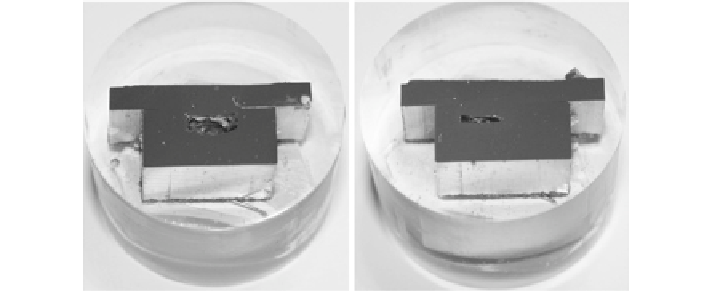