Civil Engineering Reference
In-Depth Information
Fig. 11.23
Cutting channel
surface profiles in A2 tool
steel workpiece
of this chatter condition. This can also be observed in the force profiles for the two
tests, where the EAM force profile shows less fluctuation in force than the baseline.
The chatter condition was a result of the processing parameters and was not actually
desired during the testing.
11.2.2 High-Strain-Rate Process Modeling and
Experimental Testing for EA Machining
With the observation of lower forces in EA machining, a bulk force model is
developed to predict average process behavior. The approach is to augment a tra-
ditional orthogonal machining force model to capture the modification to material
strength due to the applied electricity.
11.2.2.1 Empirical Relationship
The classical Merchant orthogonal machining model is modified by changing the
shear stress,
τ
, to account for electrical effects. The shear stress under electrical
effects was related to the forming stress under electrical effects, as found by previ-
ous EAF work. The shear stress is assumed, through Tresca material failure theories,
to be one half of the normal stress. From the EAM work of Jones et al. in 2011, the
normal flow stress of a material under electrical effects is predicted using:
−(ε −
C
)
B
A
σ
EA
=
K
′
ε
n
ε
m
exp
(11.23)
where
σ
EA
is the predicted flow stress with the application of electricity,
K
′ is
the strength coefficient,
ε
is the strain,
n
is the strain hardening exponent,
ε
is the
strain rate,
m
is the strain-rate sensitivity exponent,
is the current density, and
A
,
B
, and
C
are material-specific constants for this model [
11
].
When considering the current density, since the current varies as a function of
contact area with the shear zone, the contact area due to the formation of chips could
have an effect on the instantaneous current density. Neglecting the effect of dynamic
chip formation, the instantaneous current density during the test can be described by:
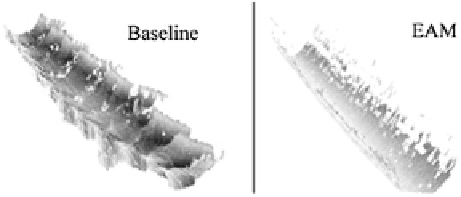