Biomedical Engineering Reference
In-Depth Information
thickness reduction [%]
13
Blank:
Material: Titanium (grade 2)
Width: 1.0 mm
Shell-Elements
Integration points: 5
4
Hydraulic pressure
Linear increase;
0-65 MPa
Solver
LS-Dyna (explicit)
max. thickness redcution:13 %
-5
Fig. 9
Results of the process simulation [
20
]
which is trimmed and connected with the universal geometry. To verify that the
designed standardized hip cup prosthesis can be manufactured by the HPF-process
a FE-simulation is carried out. Thereby all settings are taken over by the simulations
executed in [
18
].
In Fig.
9
, the results of the simulation is illustrated. It can be noted that the manu-
facturing process lead to a reduction ratio of maximum 13%. This value is even lower
compared to the results presented in Sect.
3
. This is due to the fact that for the com-
parative simulation an prothesis designed by an individual canine acetabulum was
used which differs from the standardized prothesis. This verification leads to the use
of the designed standardized hip-cup prosthesis for the transfer of the HPF-process
to real process design.
5 Outlook
For the future it is planned to extend the presented geometrical deduction method,
so that an automated identification of the cluster can be realized. Furthermore it
is planned to execute a correlation hypothesis between the cluster formation and
certain parameter. These parameter can be weight, length- and height-diameter of
the acetabulum as well as acetabulum depth. On the basis of this analysis it can be
possible to assign a potential patient to a cluster only by measuring the choosed
parameter. Additionally an increase of the original geometry number is intended to
provide a statistically secured data base.
Based on the simulations introduced in this study the design and the test of the
HPF die for the production of the standardized components will be a next step of
this project as well. With this die it is planned to produce first canin hip cups which
will be tested. Cadaver test will be executed to provide information concerning the
effort of the surgical intervention compared to the implantation of a conventional hip-
cup prosthesis. Furthermore bone remodelling simulations using the new prosthesis
design will be carried out. Finally it is planned to adapt the whole concept for human
geometries.

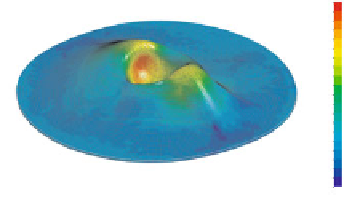
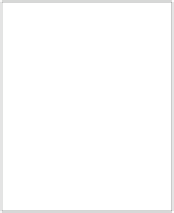



