Biomedical Engineering Reference
In-Depth Information
III.
Form bounded
forming
II.
Free forming
I.
Die closing
distance
plate
feed
blank
die insert
drawing die
Fig. 3
Process sequence of high-pressure sheet metal forming with die insert
the simulation of both forming concepts at room temperature and at 200
◦
Cusing
commercially pure titaniumgrade 2 characterized bymeans of standard tentile testing
experiments at both temperatures. Except for the HPF at room temperature, the
manufacturing of the standardized hip-cup prosthesis by means of the other forming
methods and conditions lead to a critical reduction of the sheet thickness (
25%).
Thus theHPF-process at room temperaturewas choosen for the real process described
in detail in the next section.
>
3.2 High Pressure Sheet Metal Forming
The HPF process offers, in addition, the following advantages over the punch-die
forming procedure [
19
]:
•
use of different blank thicknesses and qualities without changing the die,
•
production with less stages,
•
improvement of buckling strength as well as dimensional and geometrical accu-
racy.
In Fig.
3
the process sequence is illustrated. First the die is closed, so that blank
and distance plate are in contact. This leads to a sealed interior space. Then the fluid
is pumped into the interior space of the die through the feed in the distance plate.
During the first forming phase a free forming take place. In the second phase, the
form-bounded forming takes place, so that the blank is pressed against the contour
of the die insert.
4 Derivation of the Universal Prosthesis Geometry
To realize the manufacturing concept the development of the two-stage manufactur-
ing process is accompanied by a designmethod adjusted to the two-stagemanufactur-
ing process presented before. For the manufacturing of the standardized components,

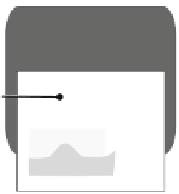

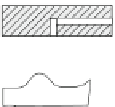
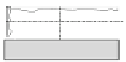

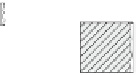





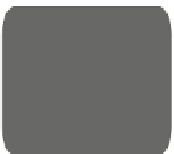
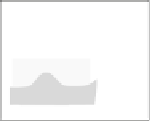

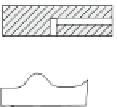
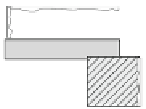









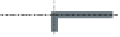

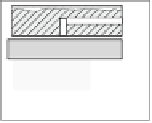




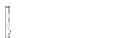









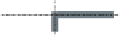
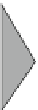


























































