Civil Engineering Reference
In-Depth Information
1
1
/
2
" min.
clear to
stirrups
(ACI 7.7.1)
#3 stirrup with #5 &
#6 bars
c
s
d
s
r =
3
/
4
" for #3 stirrups
1" for #4 stirrups
#4 stirrup with
#7—#11 bars
d
b
r
1"
d
b
(1.33) (max. aggregate size)
Minimum
c
s
clear spac
= largest of
Figure 3-5 Cover and Spacing Requirements for Tables 3-2 and 3-3
where
b
w
= beam width, in.
c
c
= clear cover to tension reinforcement, in.
c
s
= clear cover to stirrups, in.
d
b
= diameter of main flexural bar, in.
d
s
= diameter of stirrups
The values obtained from the above equations should be rounded up to the next whole number.
The values in Table 3-3 can be determined from the following equation:
b
w
−
2(c
s
+
d
s
+
r)
n
=
1
+
(minimum clear space)
+
d
b
where
⎩
3/4 in. for No. 3 stirrups
1in. for No. 4 stirrups
r
=
The minimum clear space between bars is defined in Fig. 3-5. The above equation can be used to determine the
maximum number of bars in any general case; computed values should be rounded down to the next whole number.
Suggested temperature and shrinkage reinforcement for one-way floor and roof slabs is given in Table 3-4.
The provided area of reinforcement (per foot width of slab) satisfies ACI 7.12.2. Bar spacing must not exceed
5h and 18 in. (where h = thickness of slab). The same area of reinforcement is also applied for minimum
moment reinforcement in one-way slabs (ACI 10.5.4) at a maximum spacing of 3h, not to exceed 18 in.
(ACI 7.6.5). As noted in Chapter 4, this same minimum area of steel applies for flexural reinforcement in
each direction for two-way floor and roof slabs; in this case, the maximum spacing is 2h not to exceed 18 in.
(ACI 13.3).
As an aid to designers, reinforcing bar data are presented in Tables 3-5 and 3-6.
See Chapter 8, Section 8.2, for notes on reinforcement selection and placement for economy.

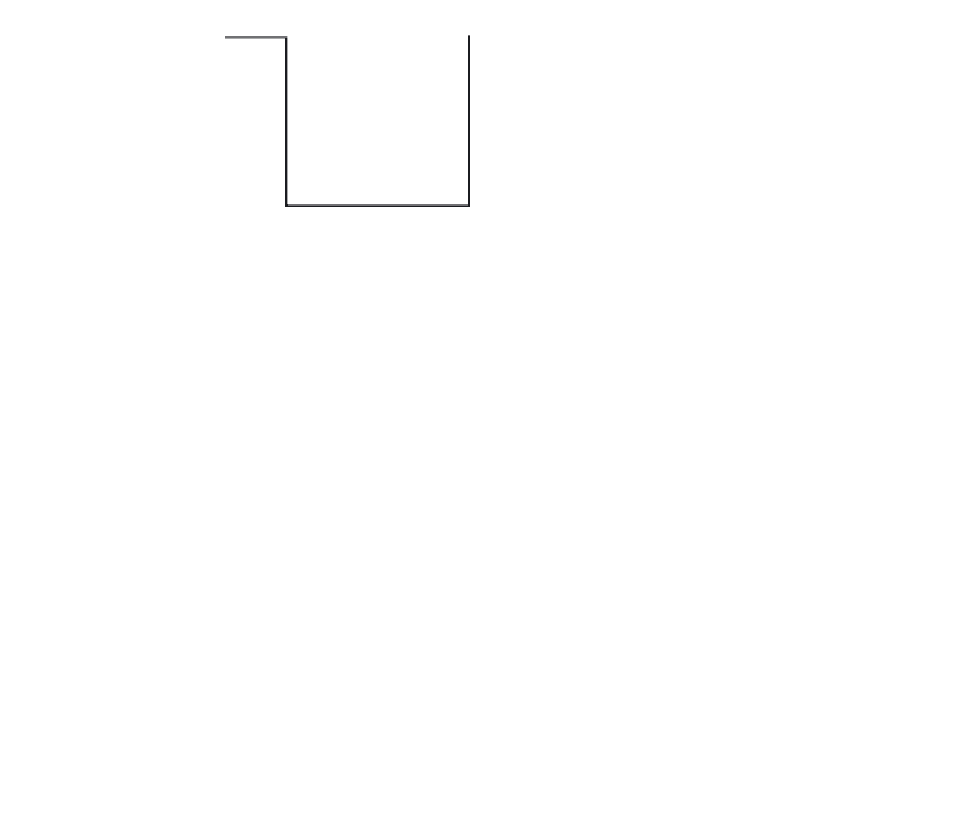
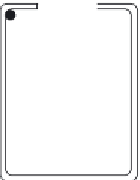




































Search WWH ::

Custom Search