Environmental Engineering Reference
In-Depth Information
0.03
0.02
0.01
0
-0.01
0.9
0.92
0.94
0.96
0.98
1
0.1
0.05
0
0
0.2
0.4
0.6
0.8
1
Distance along chord line, x/c
Fig. 7.12 Measured blade section of the Aerogenesis 2.5 m long blade from the power
producing section. Bottom graph shows whole section. The top graph highlights the trailing edge
(data from Rachel Wong). The gap in the lower surface data is due to mounting of blade section
for measurement
aerofoil, probably as a result of the way the two halves were joined. The upper
surface (with most curvature) was placed in its mould and the lower surface was
vacuumed onto it after applying the glue. It is thought that the vacuum deflected
the lower surface towards the upper one. The upper part of the figure shows an
expanded view of the trailing edge, which clearly demonstrates the technique of
manufacture. Trailing edge thickness can be a problem for small blades because of
the conflicting requirements of finite thickness for safety and integrity and minimal
thickness to reproduce the design shape and suppress trailing edge noise. This
arises from vortex shedding behind a trailing edge of finite thickness and is usually
correlated by the ratio of trailing edge thickness to the chord, it is difficult to keep
this parameter small for small blades. Nevertheless, noise calculations by Clifton-
Smith [
3
] suggest that trailing edge thicknesses of 1-3 mm are tolerable for most
small blades. No computational studies have yet been done to study the effect of
the change in shape on turbine power extraction.
Significant parts of the upper (downwind) surface of any blade will be in
compression for most of the operating life of the turbine, so it is possible that a
blade can buckle. Partly to prevent this, most large blades have a ''shear web'' or
''spar'', as discussed, for example by Burton et al. [
6
], Brønsted et al. [
7
], and
Dutton et al. [
8
]. This is a short (in the chord direction) box keeping the blade
halves apart in the region of maximum thickness. Not all small blades have a spar;
the blades of the Skystream shown in Fig.
1.2
are hollow. If used, the spar needs to
extend to the leading edge to be a glue dam or some other arrangement is
necessary.
It should be clear from this description that vacuum infusion requires care and
considerable labour and so may not be suitable for volume production by poorly-
trained workers. On the other hand, its capital cost is small, at least once the
moulds have been provided, so it a good method to make a small number of
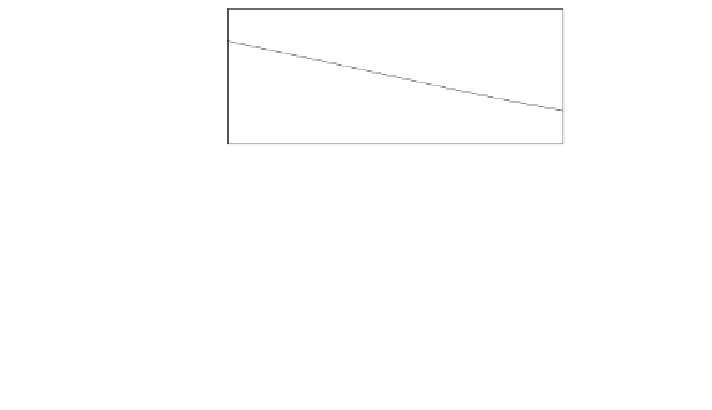

















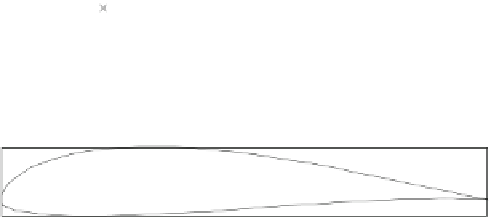


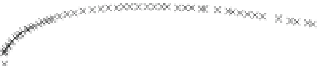







































Search WWH ::

Custom Search