Environmental Engineering Reference
In-Depth Information
Fig. 7.3 a Chord
distributions for average of
the non-dominated blades for
the values of a indicated.
Solid line shows Eq.
5.12b
and the dashed line shows
(
5.12a
). Successive plots are
displaced upwards by 0.2.
b Twist distributions for
non-dominated blades for the
values of a indicated for
Q
r
= 0. Solid line shows
Eq.
5.13b
and the dashed line
shows (
5.13a
). Successive
plots are displaced upwards
by 25
(a)
Q
r
= 0
1
a = 0.7
0.8
a = 0.8
0.6
a = 0.9
0.4
a = 1.0
0.2
a = 1.0, no tip losses
0
0.2
0.4
0.6
0.8
1
Radius, r/R
(b)
140
Q
r
= 0
120
a = 0.7
100
a = 0.8
80
60
a
=
0.9
40
a = 0.1.0
20
a = 1.0, no tip losses
0
0.2
0.4
0.6
0.8
1
Radius, r/R
hardly changes showing that starting and power production are dominated by
opposite ends of the blade.
For Q
r
= 0.5 Nm, the changes are larger and much more extensive which
indicate the significance of the resistance; note that this generator has a high ratio
of cogging to rated torque from Fig.
1.12
.
Figure
7.5
shows the optimal fitness front for both values of resistive torque and
clearly demonstrates the significance of Q
r
in determining the starting time: fur-
thermore, for Q
r
= 0.5 Nm the BET optimum blade did not start. For Q
r
= 0, the
blade for a = 0.8 with C
P
= 0.484 would be suitable for the chosen generator,
provided tight control was kept over the blade shape during manufacture to ensure
that the aerofoil profile was reproduced accurately. In terms of the most efficient
blade, the chosen design produces 4% less power but its starting time is 33%
lower. For Q
r
= 0.5 Nm, the blade for a = 0.9 with C
P
= 0.487 would be suitable.



































































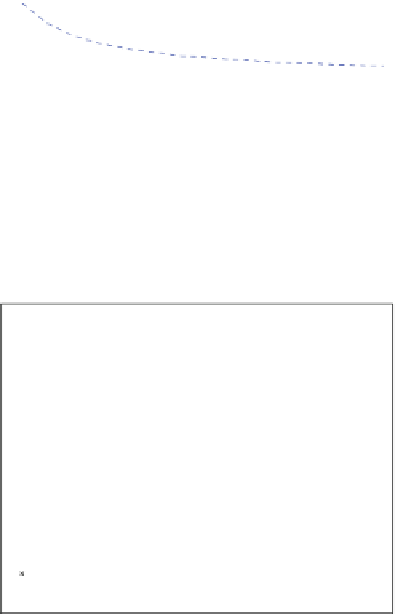




















































































































































































































































Search WWH ::

Custom Search