Environmental Engineering Reference
In-Depth Information
Commercially available cryocoolers are designed for the laboratory or hospital
environment, and would require some ruggedisation to be suitable for an off-
shore wind turbine environment. The coolers of the temperature range and power
required for the HTS generator use either the Gifford-McMahon cycle, or Stirling
cycle. Maintenance intervals are presently 9-18 months, which would need to
be extended for offshore wind power applications. Zero maintenance has already
been addressed for very small cryocoolers - there a large number small Stirling
cycle coolers on spacecraft that have operated without maintenance or failure for
up to 16 years. Newer cooler technology such as pulse tubes, which have no mov-
ing cold parts [30], and free piston Stirling cycle coolers [31], which have no
wearing seals, are beginning to become viable in the larger power ratings required
for HTS machines.
5 Developments in HTS wires
HTS generators cannot be a commercial success in the wind market without low
cost volume production of HTS wire. All HTS wire produced to date has been
more than an order of magnitude too costly to be considered. However, a new
class of HTS wires have been developed and are currently at the early stage of
commercialisation. These wires have the potential to meet the volume and cost
requirements for the HTS wind generator. These new wires have become known
as 2G HTS wire and the earlier wire as 1G.
5.1 1G HTS wire technology
Until very recently (2006) all commercially available HTS wire was based on
BSCCO and manufactured using the 'Powder in Tube' method. The HTS precur-
sor powder was placed inside a machined silver tube which was the drawn out
until reduced to about 1 mm diameter. This was then cut into short lengths and
a large number of these, typically 80-100, placed inside another silver tube, and
drawn out again until about 1 mm diameter. This wire was then rolled fl at to about
4 mm wide by 0.2 mm thick. The fi nal process was a controlled heat treatment in a
controlled atmosphere to produce the superconductor material inside the fi laments.
The resulting wire structure can be seen in Fig. 4.
This was an inherently costly process, requiring a large fl oor space for the draw-
ing process. Early wire was priced at around 1000 $/kAm, with prices in 2008
around 130 $/kAm. The ultimate minimum price in volume for this wire is
Silver Matrix
Ceramic HTS Filaments
Figure 4: Composition of 1G BSCCO wire.
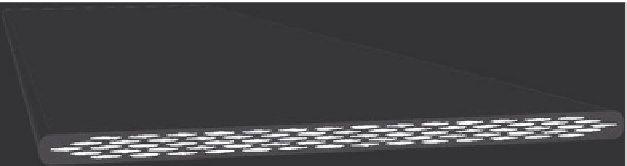




Search WWH ::

Custom Search