Biomedical Engineering Reference
In-Depth Information
Overall, the general test setups for abrasion testing are comparable to each other
and machines for testing are readily available due to the existing standards. But
the evaluation study by Guiot et al. (2009) stresses the point that small changes in
the setup and parameters, for example, rotations per minute, may have significant
influence on the test results. Some further adjustments of the current setups are also
needed to allow the quantification of the total release rates, improve the reproduc-
ibility, and ensure safety for the personnel.
12.2.4 s
CratChing
Scratching is a special case of low speed mechanical processes with a limited contact
area to the material. This process can be simulated by using, for example, a metal-
lic comb being pushed over a surface with a specific weight (Figure 12.8; Golanski
et al. 2012). Golanski et al. (2012) developed a scratching tool inducing nonstandard-
ized stresses and tested on model polymers with defined CNT content. Therefore, a
homemade stainless steel rake on Taber equipment was used. The rake had a width
of 26 mm and a teeth distance of 3 mm. The aspiration of abraded or scratched
particles was measured with SMPS and/or electrical low pressure impactor (ELPI).
Additionally, samples were collected for subsequent SEM or TEM analysis.
The scratching results showed a release of nanoscaled particles (mainly <30 nm)
from a polyvinylchlorid (PVC) fabric containing NP with negligible release from the
corresponding NO-free reference material.
Le Bihan et al. (2013) investigated the release of the nano-objects during different
operations related to the handling and processing of an automotive part. The experi-
ments were carried out in a sealed glove box testing surface scratching in three direc-
tions, surface sawing, and surface sanding (19,000 rpm). An iron alloy shaft cap with
a fullerene coating (thickness 0.1 µm) was tested. During the tests all measurement
devices (CPC, SMPS, and OPC) were fed from a unique sampling point (Figure 12.9).
The clean air inlet flow (4.5 lpm) allowed working in a nearly particle-free atmosphere.
The particles emitted by scratching were mainly in the size range of 10-500 nm
with total number concentrations of approximately 10 #/cm³. Peak concentrations dur-
ing sawing reached 1,000 #/cm³ and 900 #/cm³ during sanding (Le Bihan et al. 2013).
The sanding results showed that 50% of the released particles were smaller than 40 nm.
FIGURE 12.8
Solicitation tool used in the study: a stainless steel rake integrated into a lin-
ear Taber test. (With kind permission from Springer Science+Business Media:
J. Nanopart.
Res
., Release-ability of nanofillers from different nanomaterials (toward the acceptability of
nanoproduct), 14, 2012, 1-9, Golanski L. et al.)
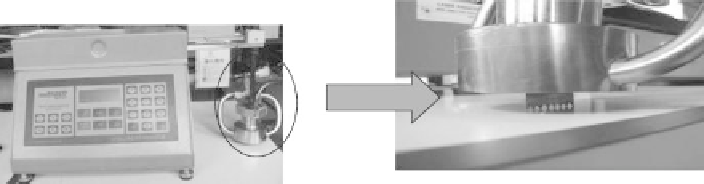
Search WWH ::

Custom Search