Geoscience Reference
In-Depth Information
Figure 14
Photo of stepped vertical face.
the grid manufacturer, proposed a radically different face comprising site-cast,
ordinary-Portland-cement concrete blocks (with 50-MPa 28-day compressive
strength). These blocks were 2.7 m long, 0.6 m high, and 0.3m wide and
contained either one or two layers of “starter” lengths of cast in Type 2 geogrid
(Fig. 12)
.
The deeply embedded thick transverse bar of the grid has been shown to
provide an anchorage in excess of the design strength of the reinforcement.
HDPE grids have been shown to be unaffected by the highly alkaline
environment associated with the concrete embedment (Wrigley, 1987).
This solution was attractive to the contractor, who had already established a
batching plant on site and estimated that he could produce blocks at about one
third the cost of typical proprietary segmental units.
For simplicity, the blocks were produced with a stepped vertical face, and
so the slope profile was amended (
Figs. 13
and 14).
These blocks overcame the need for both the shuttering and the coarse fill.
The main grid lengths were connected to the starters using bodkins, and the
geotextile was used to prevent washout of fines through any small gaps between
blocks.
The blocks were cast at a rate of up to 36 per day. Over 1000 blocks, each
weighing approximately 1 ton, were required. Installation was much less labor-
intensive when compared to Lake 1.
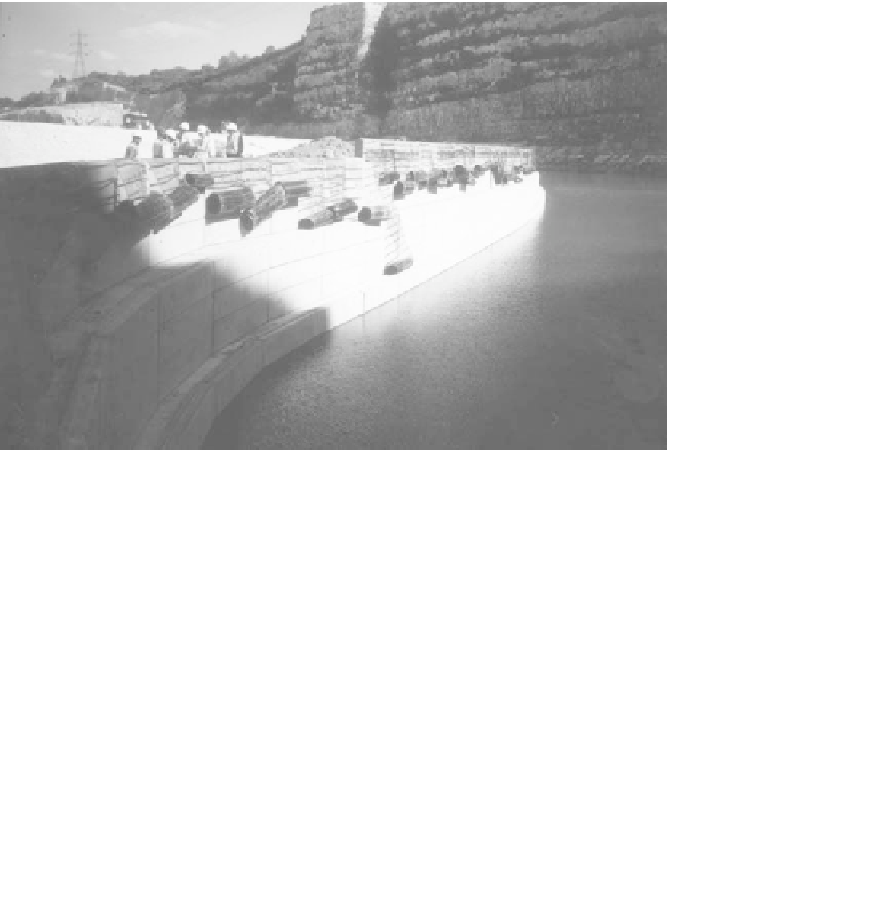








Search WWH ::

Custom Search