Biomedical Engineering Reference
In-Depth Information
Tightness
Integrity
Residual
moisture
Contamination
Cleaning
interval
Test regime or dosing regime {e.g. order
of testing or speed of sampling}
First dose effect
Through life effect
Store and test orientation
Cleaning
Analytical protocol
Diameter
Blocked
Specifications
Corrosion
Distance
Jets
Standard
preparation
Dilution
Extraction
{time,
volume,
flask}
Corrosion
Planar
Coating
Integrity
Order
Plates
Sample
preparation
Impactor
Contamination
Solvent
Mix up
plates;
flask; vials
Geometric
dimension
Opening of
pre-metered
units
Cleaning
Contamination
Type
Priming
Time
Position
Training
Number
Handling
Handling
Storage
conditions
Transport
conditions
Environmental
conditions
Flow
resistance/pressure
drop
Flow
meter/Pump/Flow
controller
Flow rate
Flow
volume
Critical flow
{P3/P2}
APSD Change
Measurement/Analytics
Device
Surface
Operator
Assembly
/Integrity
Geometry
Coating
Accessories
Adapter/SIP/HTP/Preseperator
Type
Dellvery
Injection
precision
Column
Eluent
Detector
Linearity
Equipment
Unit
Method
HPLC
Integration
Dilution
factors
Calculation
Data
transfer
{manual/electronically}
Humidity/Temp/Electrostatics
Evaluation
Fig 9.8
Potential causes for APSD changes related to the DPI. API analytics and measurement
processes (
From
[
9
]
—used with permission
)
API but also to detect or prevent changes within manufacturing or analysis of the
OIP. They found that these strategies can be subdivided into three different
categories:
1. Quality assurance and manufacturing controls
2. Product handling controls
3. Overall quality control for the OIP itself
These operate in a continuous cycle as the OIP moves through its life cycle
(Fig.
9.10
).
Glaab et al
.
[
9
] continued their analysis by examining the various control strate-
gies that can be put in place to mitigate APSD changes for both types of OIP
(Fig.
9.11
). Their hypothesis was that if all these strategies were to be adopted,
changes that could infl uence the aerosol APSD at the fi nal release testing stage
could be easily detected and mitigated or eliminated at the earliest possible stage.
If adopted, this degree of control would therefore make the application of EDA in
the life cycle of such products easier to manage [
10
].
In the fi nal stage of their evaluation, Glaab et al
.
[
9
] considered the relative mag-
nitudes that the identifi ed risk factors could lead to catastrophic product failure.
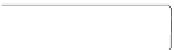


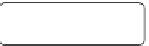


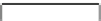

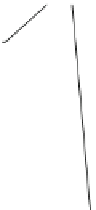

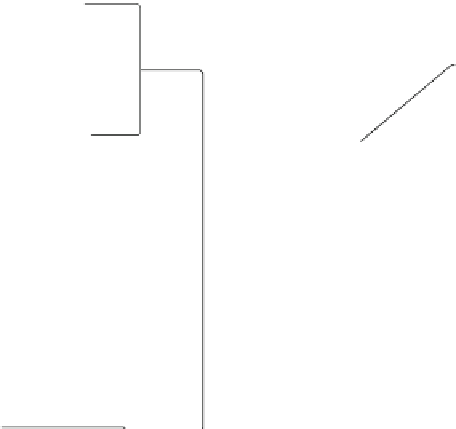
















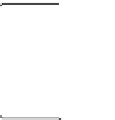
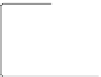












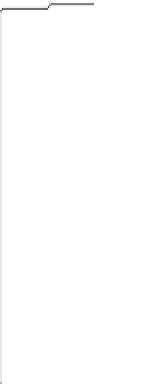


Search WWH ::

Custom Search