Graphics Reference
In-Depth Information
Figure 15.20.
Cross-section of cylinder/plane
blending with a cyclide.
Figure 15.21.
The cone/torus blending problem.
but are also more complex computationally. Shene ([Shen98]) gives a complete analy-
sis of possible blendings of two cones with a cyclide. The paper [Shen00] discusses a
solution to problems encountered with a common construction for blending two
cones with a cyclide. A well-known unsolved blending problem is the so-called Cran-
field object that involves a cone/torus blend. See Figure 15.21. The actual Cranfield
object is a real part of an oil rig. Although it is possible to model the part in com-
mercial systems, it is not easy. As Pratt ([Prat90]) and others have pointed out, mod-
eling systems should have built in capabilities that would allow a user simply to
specify the cone and torus and let the system do a robust blending operation on its
own. Other references for cyclides can be found in the bibliography.
Next, we look at blending based on parametric surfaces. A good reference is
[ViMV94]. It will be worthwhile to start with some terminology as summarized by
Vida et al.
Base surfaces:
The surfaces that are being blended. See Figure 15.22(a).
Blending surface:
The surface that does the blending. See Figure 15.22(a).
Trimline:
A curve along which the base and blending surfaces meet.
Such a curve can be considered as a curve that trims the
base or blending surface. See Figure 15.22(a).
Range parameter:
Parameters that specify the extent of the blend such as how
far from the intersection of the base surfaces the trim line
should be. They could be computed automatically or speci-
fied by the user. See Figure 15.22(b).
Spine curve:
In those cases where a blending surface is defined by a
sweeping-type operation, a spine curve could be the trajec-

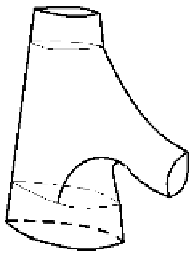
