Information Technology Reference
In-Depth Information
Interfacing
of AC-DC power converter control
and galvanic insulation
Gate impulses
Th1
Th2
.
i
s
ˉ
.
Thyristors
gate drive circuit
∼
v
DC
v
s
motor
.
Load
D3
D1
D2
D
T
Tachometer
Interfacing
of acquirement and adaptation
of speed DC motor
Data Acquisition
and Control System
Fig. 11 The proposed experimental setup schematic for DC drive control
polarization bridge constituted by a resistor and two 1N4148 diodes in series. This
transistor acts as a current sink, whose value can be determined by an adjustable
emitter resistor, to make the capacitor be fully charged after exactly 10 ms. The
obtained synchronous saw-tooth signal is compared with a variable DC voltage,
using an LM393 comparator, in order to generate a PWM signal which drives a
NE555 timer, used as an astable multi-vibrator, producing the impulse train needed
to control the thyristors
firing. This impulse train is applied to the base of a 2N1711
bipolar transistor which drives an impulse transformer that ensuring the galvanic
isolation between the control circuit and the power circuit.
The nominal model of the studied plant and the controller model obtained in
synthesis development phase were used to implement the real-time controller. The
model of the plant was removed from the simulation model, and instead of it, input
device drivers (sensor) and output device driver (actuator) were introduced as
shown in Fig.
12
. These device drivers close the feedback loop when moving from
simulations to experiments. According to this concept, the Fig.
13
illustrates the
Fig. 12 Synoptic of the
PCI-1710 based real-time
controller implementation
Simulation procedure
Plant model
Controller model
Real-time application
Controller model
Input Driver
Output Driver

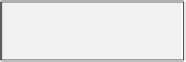




























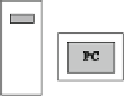



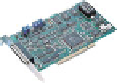
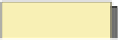
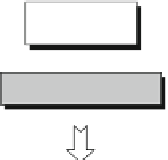

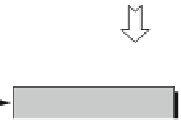




























































Search WWH ::

Custom Search