Global Positioning System Reference
In-Depth Information
Z
Vibrational modes make
force generated by rotation
perpendicular to ceramics
X
Ω
Y
Ceramic used
for feedback
Two ceramics
used for driving
and detection
Elastic invariable
metal
Figure 9.26
Gyrostar free-free bar and ceramics. (
From:
[29]. © 2000 University of Calgary.
Reprinted with permission.)
The illustrated bar has a triangular cross section, with the bar faces forming an equi-
lateral triangle. Two sides are used for driving the beam at a resonant frequency and
detecting the Coriolis force; the third face is used to close the vibration control loop.
Returning to Figure 9.25, several conclusions relative to temperature sensitivi-
ties can be drawn from just these two gyro samples. First, the temperature sensitiv-
ity can be very large. For the sample denoted EM 0, the sensitivity is roughly linear
over the temperature range, and its magnitude is 0.07º/sec/ºC. If the sensitivity is
ignored, and the gyro is in an agile temperature environment (e.g., a car left outside
overnight in the winter in Boston heating up), the gyro will require frequent calibra-
tion. At constant speed, an uncompensated gyro bias error will produce a quadratic
growth in cross-track position error proportional to the product of the bias and the
speed of the vehicle. Second, the temperature sensitivity is individualized to each
gyro (i.e., if compensation is desired, every gyro must be tested prior to installation
in the vehicle, unless this requirement is levied upon the manufacturer). Such
requests inevitably increase the cost of the gyro. The sample denoted EM 4 has a
nearly sinusoidal variation, which is relatively minor over the temperature range
tested. Given a temperature curve for a gyro or accelerometer bias or scale factor, it
is tempting to use a curve fit or other means to compensate its output in real time.
There are several issues here, in addition to the expense associated with the curve fit
generation for each gyro sample. First, a temperature sensor will be needed to per-
form the compensation, and the sensor must certainly be installed near the gyro or
accelerometer sensitive element. Although some sensor assemblies may provide
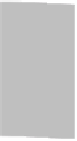




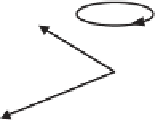
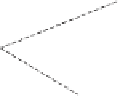




Search WWH ::

Custom Search