Biomedical Engineering Reference
In-Depth Information
(a)
(b)
0.25
ยต
m
(c)
(d)
Figure 9.25
TEM micrographs of bacterial cellulose (a), cellulose/pectin (b), cellulose/
xyloglucan (c) andcellulose/pectin/xyloglucan(d) (59) (Withkindpermission fromSpringer
Science
BusinessMedia:Planta,Mechanicalpropertiesofprimaryplantcellwallanalogues,
215, 2002, 989-96,Chanliaud, E.;Burrows,K.M.; Jeronimidis,G.;Gidley,M.J, Figures3, 6
and7.)
+
strength and stiffness to the nanocomposite compared to the neat BC (Figure 9.20). The
BC/pectin/xyloglucan nanocomposites were also prone to creep, thus exhibiting a time
dependent behavior that was not present in the BC and in the BC/pectin nanocomposites
(Figure 9.20). In fact, regardless of the loading mode, the ternary nanocomposites exhib-
ited a behavior intermediate to that of the BC/pectin and BC/xyloglucan nanocomposites,
with a closer resemblance with the later. Besides, as for the BC/xyloglucan nanocom-
posites, the ternary nanocomposites could not be modeled as linear elastic materials.
9.5.5
BC/Lignin Nanocomposites
Other model nanocomposites based on BC have also been prepared to study the lignifi-
cation of the cell wall (62, 63). Using a diffusion cell, coniferyl alcohol, a precursor of
lignin, was polymerized into a BC mat and a BC/pectin mat. Observation of the compos-
ites by SEM showed that the dehydrogenation polymers (DHP or synthetic lignin) formed
ovoid aggregates, a few microns in diameter, on the cellulose microfibrils, demonstrating
phase separation between cellulose and lignin (Figure 9.26) (62). In contrast, DHP syn-
thesized in the BC/pectin mat appeared to be more homogeneously dispersed, forming
smaller aggregates on the cellulose fibrils (62).
Pectin was thus proposed to act as a

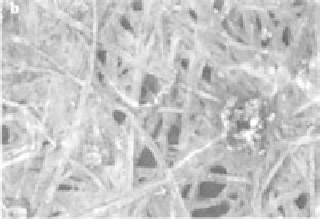
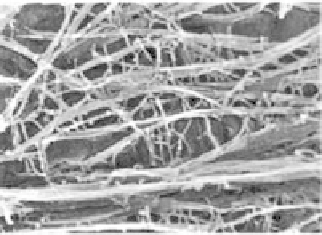

Search WWH ::

Custom Search