Biomedical Engineering Reference
In-Depth Information
on the oral tissues, it has become apparent that there are large discrepancies between their mechanical
behavior and those of most synthetic materials, in terms of viscoelasticity, anisotropy, and effects due
to the hierarchical structures and so on. As such, the conventional method for interpreting nanoinden-
tation data is inadequate for biological tissues. Consequently, different strategies have been devel-
oped to overcome some of the problems encountered in nanoindenting oral mineralized tissues, and
selected examples are discussed in the following sections.
16.2
BASIC DATA ANALYSIS PROTOCOL FOR NANOINDENTATION
Currently, most of the nanomechanical experiments published in the literature concern applications
of the nanoindentation technique, in either its basic mode involving depth-sensing indentation on a
flat specimen surface or other modified modes involving using the nanoindenter as a force-application
device to deform specimens with more complex shapes such as micro-cantilevers or micro-pillars.
Indentation testing is a well-established technique whereby a hard tip of a known geometry is pressed
against a flat specimen, and “depth-sensing indentation” which refers to an indentation procedure dur-
ing which the force and tip displacement data are continuously logged. “Nanoindentation” refers to
depth-sensing indentation with depth resolution in the nanometric regime. Before discussing issues
pertinent to oral mineralized tissues, it is useful to briefly summarize here the basic principles of
nanoindentation and the conventional data analysis method developed for hard, synthetic materials.
Figure 16.1A and B
illustrates a typical nanoindentation test and the associated load-displacement
graph respectively. In the most basic test mode, the indenter tip is made to slowly approach the
surface to be indented, and upon contacting the latter, a triangular or trapezoidal load function is
deployed for indenting the specimen. The sample is loaded, usually at a constant rate, until a maxi-
mum load is reached. A holding period may be applied at the maximum load, followed by unloading
(A)
(B)
Berkovich tip
P
max
h
max
h
c
Sample
S
=
d
P
d
h
h
max
Displacement, h (nm)
FIGURE 16.1
Schematic representation of (A) the tip-specimen contact at the maximum load
P
max
(
h
max
maximum indentation depth and
h
c
contact depth); (B) a typical load-
displacement curve generated from nanoindentation with a sharp Berkovich tip.



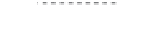







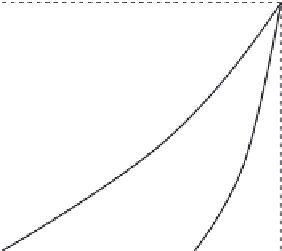







