Biomedical Engineering Reference
In-Depth Information
e
(4.49)
R
»
2
2
After substitution of (4.49) and (4.48) in (4.47), the pressure difference between
the drop interior and exterior is
æ
cos
θ
1
ö
0
(4.50)
D =
P
2
LG
γ
-
-
ç
÷
è
ø
δ
e
Equation (4.57) indicates that the pressure inside the drop decreases when the
vertical gap
d
increases. The lowest possible pressure difference is zero, so that we
find the maximum vertical gap
d
lim
defined by (4.46).
Equation (4.46) produces a rule for scaling up or down covered EWOD devices:
if the ratio
d
/
e
is kept constant, and the same materials are used, drop division will
still be possible. Equation (4.46) also confirms that a very hydrophobic contact
angle is best for the efficiency of drop splitting. In the typical case of
e
= 800
m
m,
and
q
0
= 115°, then the vertical gap
d
should not exceed a value of about 340
m
m.
Droplet Dispensing
At the beginning of any EWOD process, microdrops have to be extracted from a
reservoir. This step is called droplet dispensing [30, 31]. In the following section we
investigate the conditions for satisfactory droplet dispensing.
First, we observe that experimental and numerical simulations show that drop
dispensing in an open EWOD system is not possible for usual buffer fluids (aqueous
solutions and biological buffers). In consequence, we analyze the dispensing in a
covered EWOD microsystem. As shown in Figure 4.32, to be effective, dispensing
is constituted by three steps:
1. Liquid is extruded from the reservoir onto the electrode row by applying
an electric potential on the electrode row and by switching off the reservoir
electrodes. Extrusion occurs because there is an electrowetting force driving
the liquid onto the electrode row and a hydrophobic force pushing the liquid
out of the reservoir.
2. A pinching effect shrinks the liquid filament at the level of the cutting elec-
trode when this latter has been switched off. This pinching effect has already
been analyzed in the preceding section. This pinching step is sometimes
enough to separate a droplet from the reservoir, but it has been observed
that a third step, called the “back pumping” step was useful to easily extract
well calibrated droplets.
3. Final dispense is obtained by “back pumping” the liquid into the reservoir
after reactuation of the reservoir electrodes. The role of back pumping is to
decrease the droplet pressure so that pinching becomes more effective.
It has been checked that the dispense process is facilitated if the reservoir is
separated from the processing electrodes by a solid wall made of plastic. Simula-
tion results obtained with the Evolver software are very close to the experimental
results and confirm the key role of back pumping for drop dispense (Figure 4.33).
In fact, back pumping consists in switching the contact angle from a hydrophobic

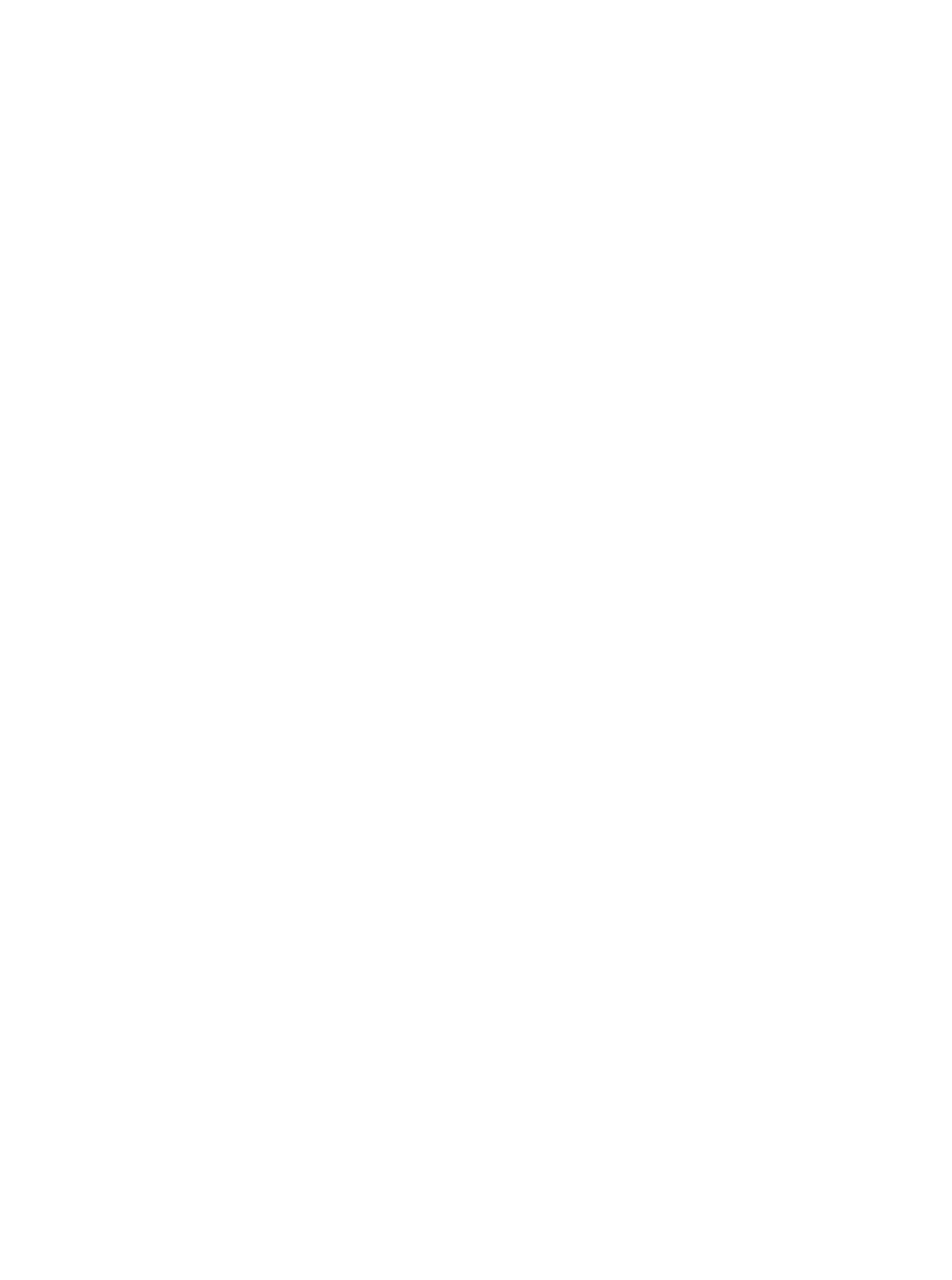
