Agriculture Reference
In-Depth Information
Table 9.5.
Variation of nut weight and copra content of hybrid crosses developed in Sri Lanka.
Cultivar
Husked Nut (g/Nut)
Copra (g/Nut)
Nuts Equivalent/MT of Copra
Open pollinated (
Ta l l
)
821.5
197.8
5060
CRIC 60 (
Ta l l
×
Ta l l
)
832.5
201.2
4970
CRIC 65 (
Ta l l
×
Dwarf
)
692.7
178.5
5600
CRIC 65 (
Dwarf
×
Ta l l
)
711.2
180.6
5540
CRISL 98 (
Ta l l
×
San Ramon
)
1293.8
282.5
3540
Source: Marikkar et al. (2004).
Storage of copra
Moisture content is crucial for the storage stability of copra.
If the moisture content is below 6%, copra may become
fairly resistant to microbial invasion as well as rancidity.
Improperly processed copra is susceptible to microbes, such
as
Rhisopus
spp.,
Aspergillus
spp., and
Penicillium
spp., as
well as insects. At times, the microbial growths might lead
to the deposition of aflatoxin in copra. The aflatoxin residue
could even be passed on to coconut oil during oil extraction
and a part of it might also be retained in the defatted kernel
residue (Samarajeewa, 1975).
Before shipment to the retail market, processed copra is
packed in gunny bags or other suitable packaging material.
Appropriate packaging is important because the unpacked
copra can reabsorb moisture from the environment and pose
a risk from microbes, as well as insects. This might become
a severe problem, especially during rainy seasons. The dried
copra stored in alkathene-lined gunny bags remains in good
condition than that stored in ordinary gunny bags. For large-
scale storing of copra, the use of dehumidifiers is suggested
as an effective method to control humidity during storage
(Anon, 2006). Recent developments in vacuum packaging
technology may be also adaptable to improve the shelf life
of edible copra as it may reduce the chance of moisture re-
absorption and oxygen contact during the storage of copra.
spoiled nuts, immature nuts, and partially germinated nuts
are screened out (Kumar et al., 2003). The DC process-
ing involves a series of steps such as deshelling, paring,
washing, disintegrating, desiccating, grading, and packing
(Kumar et al. 2003).
Deshelling
Deshelling involves separation of kernels from the nut
shells. In conventional DC processing plants, deshelling
is often performed manually by skilled laborers, while
modern plants employ mechanized deshelling operation.
The personnel involved in deshelling are called
hatcheters
;
a skilled hatcheter can deshell an average of 3,000 nuts
per day.
Paring
After deshelling, the kernel with the dark brown testa is
ready for paring. Paring is the process of peeling off the
thin brown testa covering the kernel. It is done manually
using paring knives and requires skilled laborers. In the
conventional DC manufacture, an average of 18% kernel
is lost during paring operation. After peeling, the white
kernel can be split opened to release water inside the nuts.
With this, the wet kernel would be ready for washing and
sterilization.
Washing and sanitation of wet kernel
After removal of nut water, the pared kernel is washed
thoroughly to remove any dirt. After washing, the kernel
pieces are sanitized in boiling water for a few minutes in
order to eliminate any microbial contamination.
Desiccated coconut processing
Desiccated coconut (DC) is another dehydrated form of co-
conut kernel. In most countries, it is processed primarily to
meet the export demand from the Western Europe and the
United States. Despite its use as a substitute for fresh ker-
nel, it finds many applications in the confectionery indus-
try as a food ingredient. Unlike copra, DC is manufactured
more hygienically using modern food processing facilities.
Strict quality control measures are taken from the point of
nut selection to packaging the finished product. As a pre-
requirement, coconuts need to be subjected to seasoning
for a period of 5-6 weeks. In the raw material selection,
Pulverization of wet kernel
Cleaned kernel pieces are passed through a disintegra-
tor by screw-type conveyers. Disintegrator is a machine
equipped with a series of adjustable points and blades on a
revolving drum, which pulverize bigger pieces of the ker-
nel into smaller particles. Both the disintegrator and the
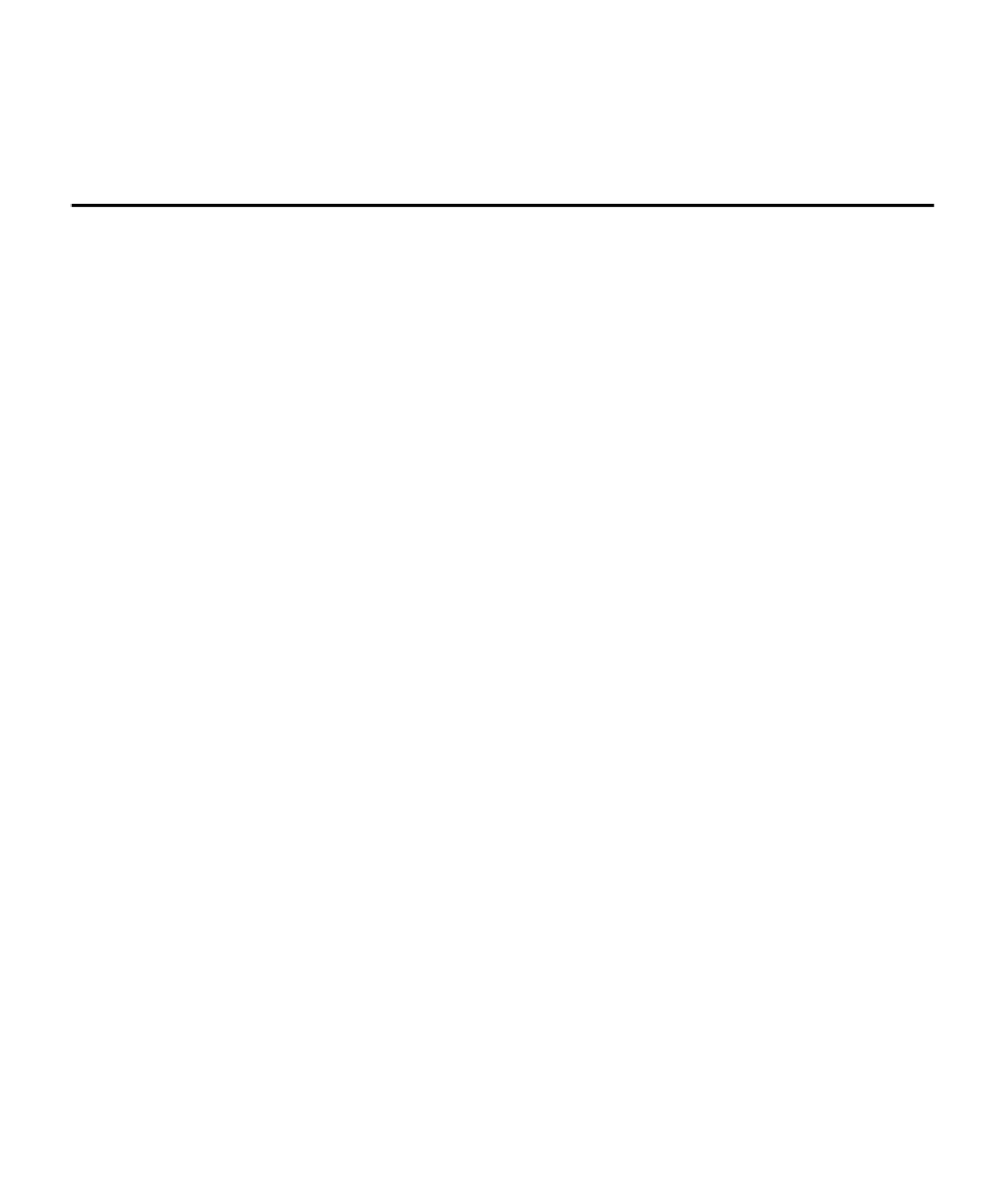

Search WWH ::

Custom Search