Environmental Engineering Reference
In-Depth Information
After 1985, manufacturers and operators started programs to
rebuild, modify, restore or repair their turbines. This was to bring
failed wind farms back to operation, make revenues and improve
the image of wind energy that sufered substantially after the failure
of thousands of wind turbines across California. “Retrofitting”
became a famous term describing the exchange of wind turbine
components for overall improvement. Components exchanged were
mostly blades but also gearboxes, generators, nacelle covers and
other parts.
A good example of a highly serious technical problem was
the shutdown of a cumulative 1 000 Micon turbines in the San
Gorgonio Pass between 1987 and 1988. Due to blade failures several
wind farm blocks, each consisting of hundreds of Micon machines,
were brought to a halt—one after another. The Micon turbines,
rated at 108 kW, used Danish made AeroStar blades that either
showed cracks in the blade root or improperly working tip
brakes [2, 4]. For millions of US dollars, the blade tips were
fixed, faulty components were exchanged and the industry had
learned another hard lesson. Such technical improvements
remained a common practice in the 1990s up until today.
Figure 23.8
Danish Micon 108 kW, Tehachapi, 2010 (Photo: Arne Jaeger).
Another new challenge for American and European manu-
facturers were Asian manufacturers like Mitsubishi or Sumitomo.
Mitsubishi started its own development in 1980 without any
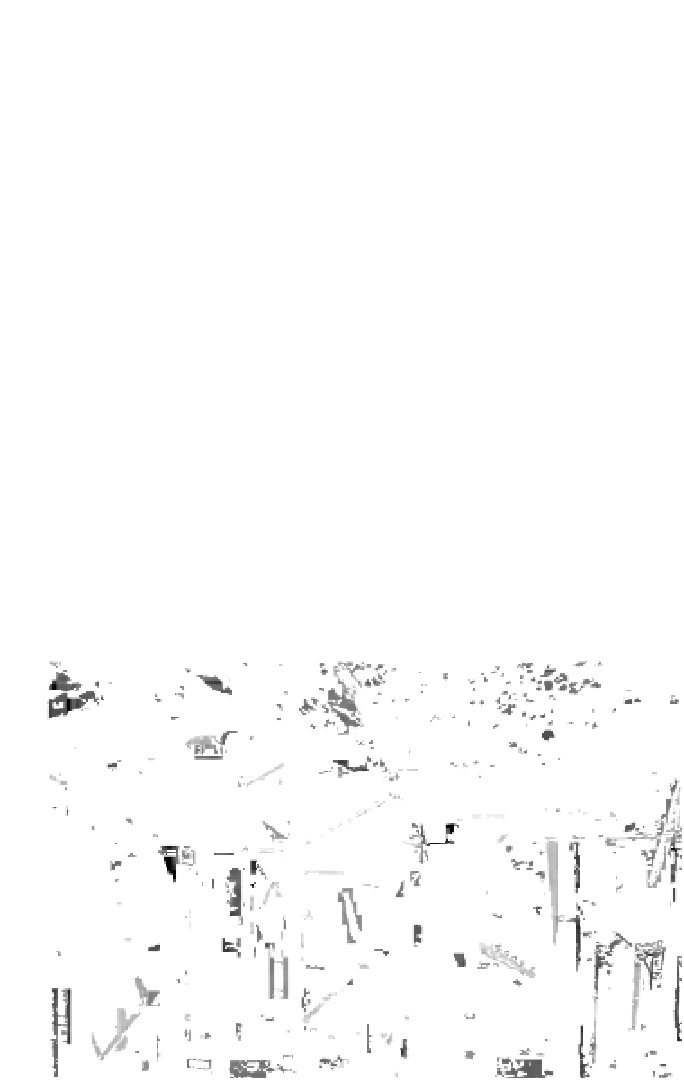


Search WWH ::

Custom Search