Environmental Engineering Reference
In-Depth Information
After considering this question, I responded—exactly how
hydraulic excavators are functioning. Then things took of. I went
with Karstensen to visit the grand old engineer and owner of LM
Blades, Mr Skouboe, who, despite his position, preferred working
in the workshop rather than at his mahogany desk. We ended up
with the first hydraulic wing brakes, which were installed for the
first time ever in the Vind-Syssel prototype. This was a revolution
in the WTG industry at that time, and it was an important parameter
of making LM into the world leading blade manufacturer.
It is of high importance that a WTG is producing maximum,
and when it stops due to too high wind speed or due to any failure, it
is important to get restarted as soon as possible.. Therefore, I wanted
Vind-Syssel to introduce a remote control based on telephone
connection to the WTG. I asked Per Gravesen, my friend and electro
technician, to make a prototype. He succeeded so well, that he later
supplied this system to the Vestas WTGs for several years. Now his
company is the leading supplier of remote control systems for
Danish water plants. Also in this matter Vind-Syssel was a pioneer.
11.7
Vind-Syssel's First Manufacturing Facilities
in Jerslev
Outsourcing of the manufacturing of components was, and still is,
appropriate in the WTG industry. Outsourcing of the erection was
also natural, as this takes a special expertise and mentality to work
with heavy cranes in the field with diferent weather conditions.
After finishing the first four nacelles, outsourcing of the assembly
work turned out to be problematic for several reasons. One reason
was that it was important to have a close and direct communication
between the workshop and the engineering and management. So,
we decided to establish our own assembly factory in Jerslev, where
our office was situated. We found a former garage for farming
machines, which could be changed into an assembly hall within a
reasonable budget, and with space for assembling of six nacelles at
a time. We also established our own service department, and we
were now really ready for takeof.
The next six units of 50 kW WTGs were sold, assembled and
erected, and we continued with the next six units and so on. At the
same time, we started developing a 200 kW version, still working

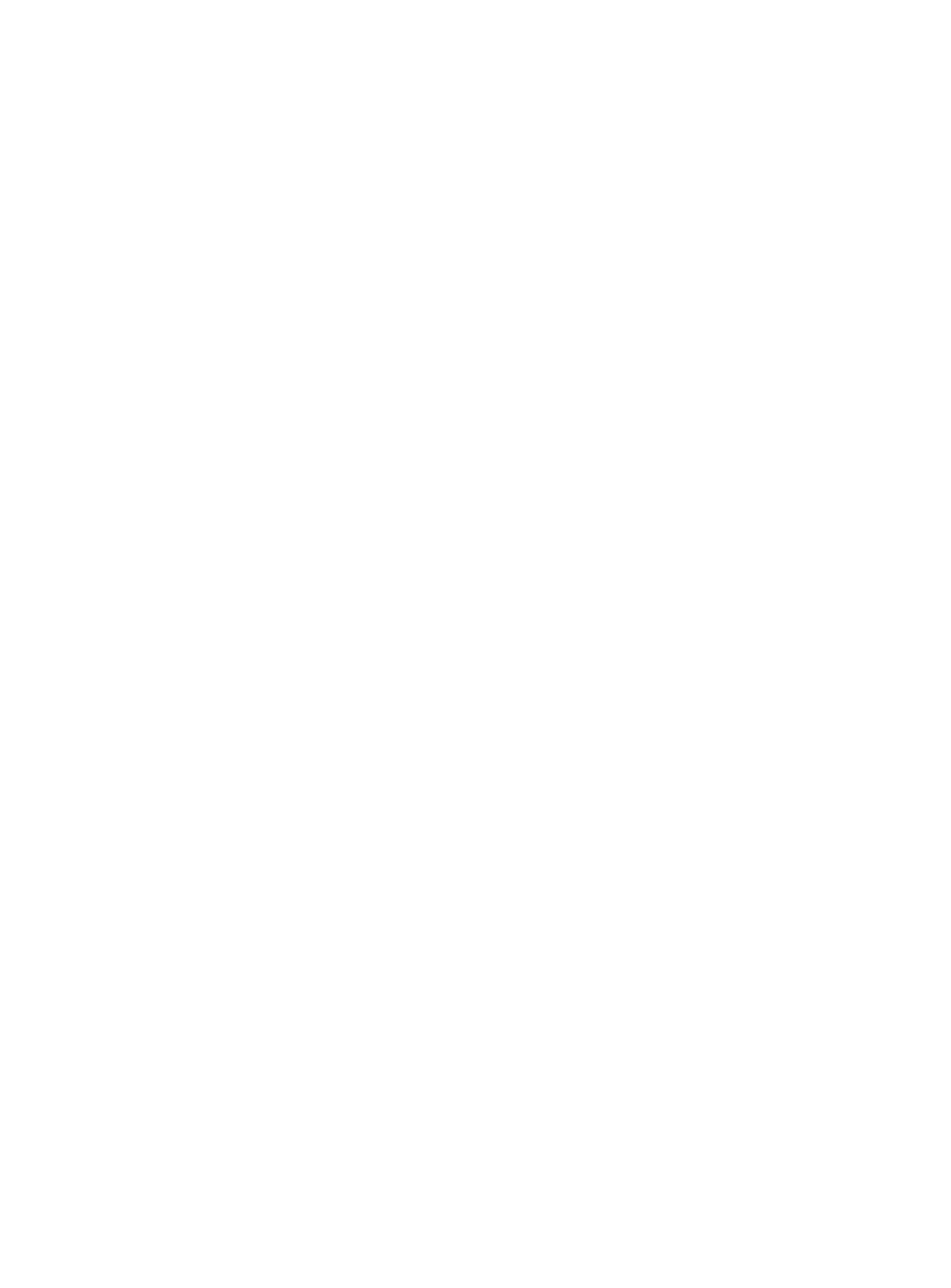
Search WWH ::

Custom Search